Ceramics are one of the oldest artifacts cherished worldwide. In Japan, Satsuma pottery was heavily exported during the nation's early modern years. Pieces of satsuma pottery, which hails from their namesake region in southwestern Japan, were highly valued for their colorful glazes and intricate designs.To take a closer look at the beauty of Satsuma’s pottery wares, we have visited Kagoshima, where the tradition of pottery remains strong.
Satsuma Pottery: Kagoshima's Centuries-Old Craft
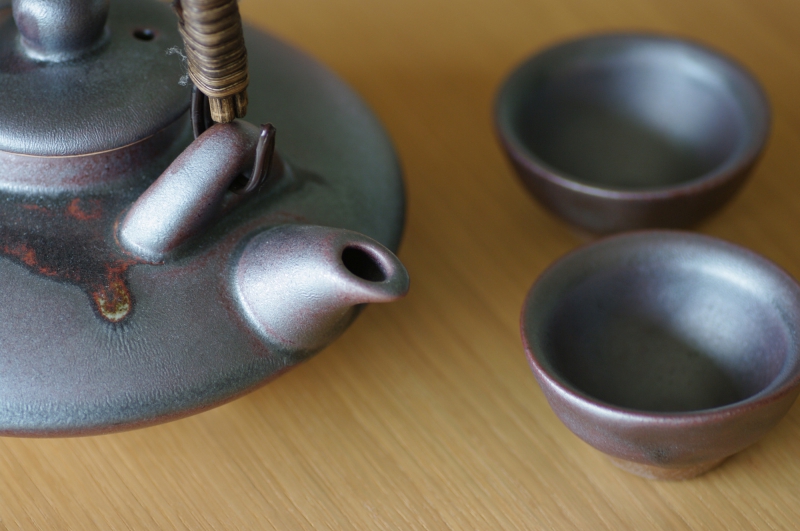
Satsuma ware: the pottery that represents Kagoshima
Satsuma pottery is a type of earthenware from Kagoshima, in southwest Japan, with a unique history and characteristics that are distinctly different from other Japanese pottery.
Let's explore two important aspects of Satsuma ware; its black and white colors, and the role of Korean potters in its history.
Black & White Satsuma Pottery: A History of Trade & Class
Satsuma earthenware is uniquely different from other types of traditional Japanese ceramics. Satsuma ware focuses on two main colors -- black and white.
"White" Satsuma ware dates back to the early Edo period, around 400 years ago. In Kagoshima, these pieces are belovedly known as "shiro-mon" which literally means "white item." Made from rare materials and decorated with delicate patterns, these white wares were favored among Japan's ruling class. White Satsuma pottery later become one of Japan's main exports, and were highly praised by Europe's noble and rich.
Traditional white Satsuma pottery was made from rare clay found only in certain areas of the Satsuma domain, known today as Kagoshima Prefecture, in Japan's southwest.That made white Satsuma pottery were highly sought after pieces. White Satsuma's delicate appearance is created by the fine cracks running across the glazed surface. These cracks called kan-nyu are intentionally formed by the differing rates of contraction between the clay and the glaze. In the field of pottery, cracks are often considered as flaws. However, the hairline cracklings only elevated the beauty of White Satsuma pieces .
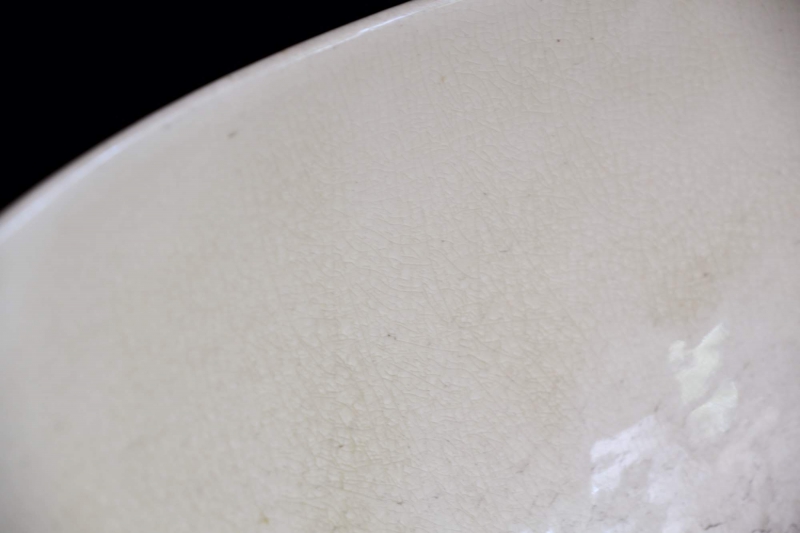
Perfect imperfections: White Satsuma's fine cracklings
Meanwhile, commoners used "black" Satsuma -- or "kuromon" (black item) -- which predates white Satsuma ware. While some black Satsuma pieces were used for tea ceremonies or treasured by powerful warlords, black Satsuma was mostly everyday ware. The dark and bulky earthenware is starkly different from elegant White Satsuma ceramics, but have an equally alluring appeal.
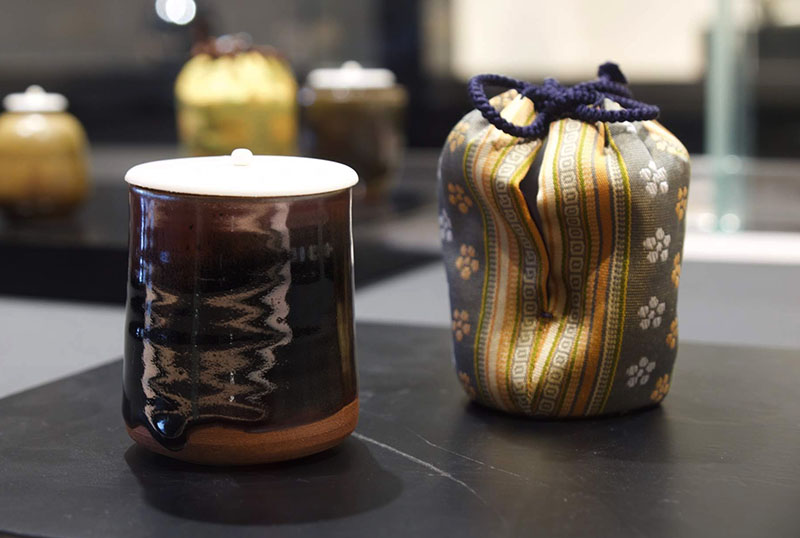
Bulky black Satsuma ware
The Korean roots of Satsuma Pottery
Satsuma pottery can be traced back to the end of the 16th century, when the Japanese ruler Toyotomi Hideyoshi launched two attempted invasions of the Korean Peninsula. The Satsuma leader Shimazu Yoshihiro was among the many feudal lords who took part in the campaigns between 1592 and 1598. When it was over, the Satsuma leader brought back home about 80 Korean potters, who settled within his domain.
Satsuma pottery was created by Korean potters brought to Japan by the Satsuma ruler
The Korean potters were given land and samurai status and began creating various types of pottery for the ruling class and commoners.
The Birthplace of Satsuma Pottery, Miyama
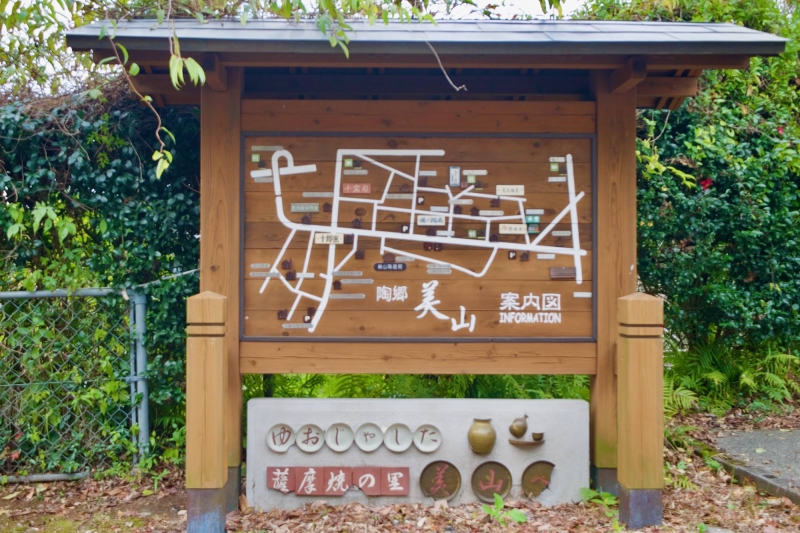
Miyama: the pottery village
For centuries, the Miyama district has been the main production center of Satsuma earthenware. It is located in Hi-oki city, in Kagoshima Prefecture.
Miyama district
Many of the Korean potters who were brought to Satsuma were later relocated to an area called Nae-shiro-gawa. This gave rise to a style of Satsuma pottery called Nae-shiro-gawa-kei (style), which covers an extensive range of high quality pottery of both black and white Satsuma ware. During its heyday, the area was home to about 18-hundred residents, who were mostly involved in Satsuma ware production.
In 1956, Nae-shiro-gawa was renamed Miyama. Today, 10 kilns stand within an area of a radius of about 600 meters, sharing climbing kilns and workshop venues. The small neighborhood is also home to many historical sites linked to Satsuma pottery.
The village also hosts glass, woodcraft and guitar studios, as well as cafes, galleries and retail shops.
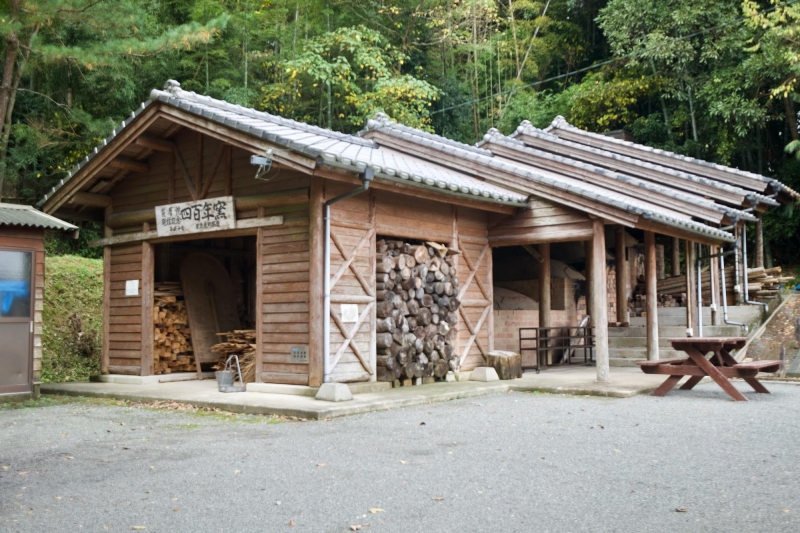
Climbing kiln co-operated by Miyama's potters
Miyama hosts unique events linked to its tradition. Every November, the Miyama Kiln Festival takes place -- an event that attracts more than 50-thousand visitors from across Japan. Visitors can purchase Satsuma ware, and sample fresh bread baked in the village's kilns.
Inheriting Satsuma Ware's History: Chinju-kan Kiln
Chinju-kan gama (kiln) is the oldest of Miyama's kilns.The Chinju-kan kiln has been run by the same family for more than 400 years, spanning 15th generations.
On the day we visited, Mr Naoki Kodama was our guide. A skilled artist himself, Mr Kodama is in charge of firing the climbing kiln.
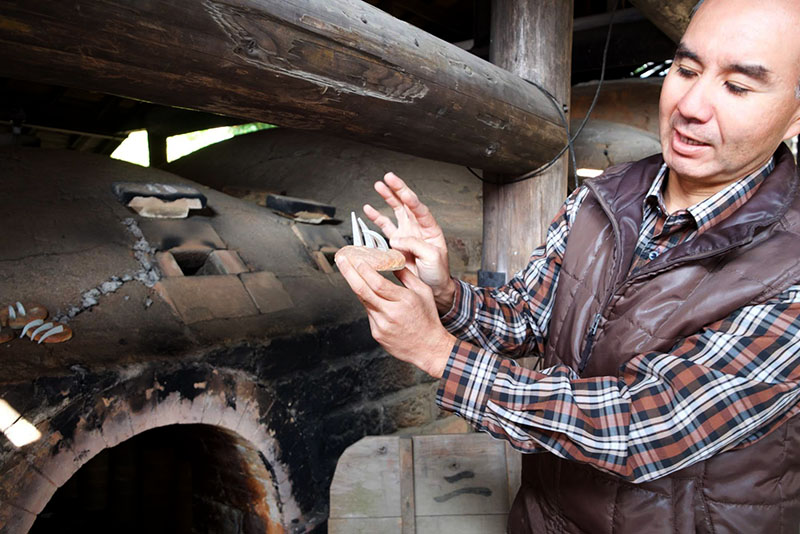
Mr Kodama is in charge of firing the kiln
We first visited the kiln museum which exhibits historical documents and Satsuma pieces from the Edo and Meiji periods. These include a fascinating collection of intricate works by the 12th Chin-ju-kan head.
Sadly, photos are not allowed inside the museum. Make sure to drop by the museum to view the breathtaking artwork.
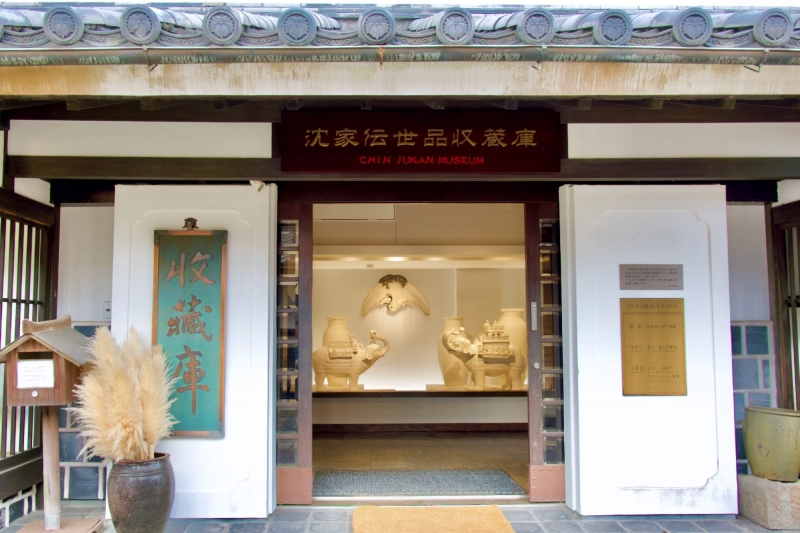
Chin-ju-kan museum exhibits historic documents and Satsuma ware
The kiln shop is an ideal place to find everyday Satsuma tableware, or home decor. A variety of both white and black Satsuma ware are offered.
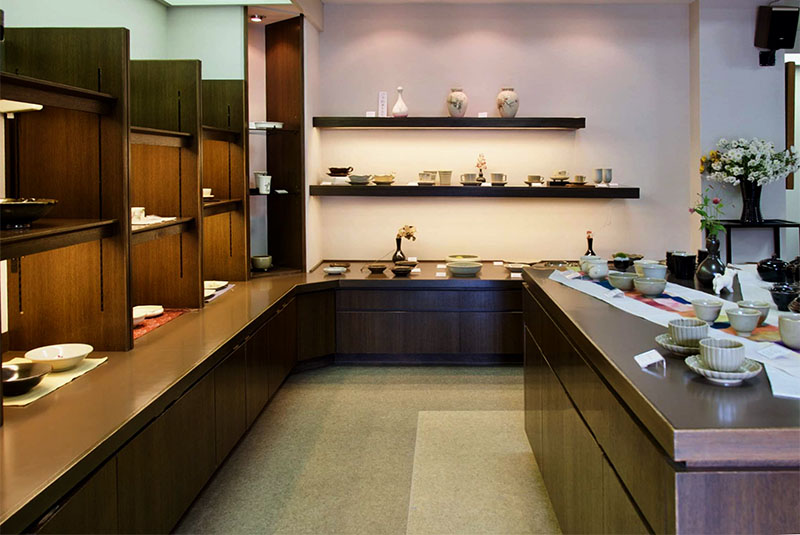
The shop has both white and black Satsuma ware
The kiln's fire continues to burn
The museum is near a climbing kiln that remains active. Climbing kilns are multi-chambered kilns built along slopes, fueled by firewood. The kilns were introduced from China via the Korean peninsula, and built across Japan during the Edo period. The labor intensive kilns are increasingly disappearing, as gas-fueled or electric kilns have become widespread.
Nowadays, Chinju-kan kiln also relies on electric kilns for firing. However, Mr Kodama says climbing kilns are still needed for a reason. The flames and ashes released inside wood-burning kilns create an effect known as yohen, which loosely translates as "kiln accident." This is an unpredictable effect that artisans are unable to control. Climbing kilns are still used to fire special works such as tea cups for tea ceremonies.
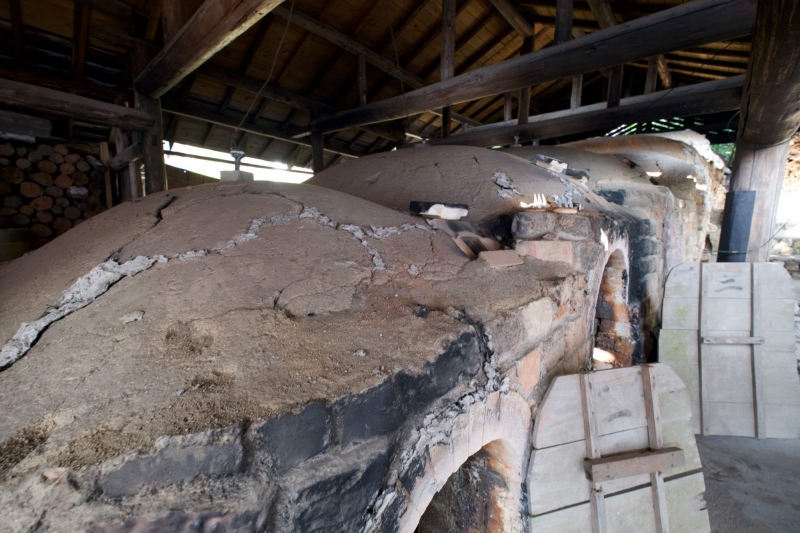
Active climbing kiln
Labor distribution in Satsuma ware production
In the past, the production process was split up into different work tasks. Labor division was necessary for two reasons.
Firstly, it was designed to protect skills. Satsuma ware was heavily protected under Satsuma rule, including its production techniques. Potters were assigned different tasks to prevent them from learning the entire production process. This meant if they were ever recruited by rival domains, they only had limited skills to take with them, and were a minor threat to their former employer.
The second reason for dividing work was improving efficiency. Satsuma pottery was Japan's cash cow export during the Meiji period. White Satsuma was particularly popular with Europeans, and Japan struggled to keep up with demand. Splitting up work helped boost output and work efficiency.
Chinju-kan kiln also separates its work. In this room, artisans works with two potter's wheels -- one each for white and black Satsuma ware.

Shaping black Satsuma with a potter's wheel
In another room, potters shape figures. This intricate process involves shaping the clay and attaching it to the vessel.
In this room, artists are assigned with openwork, or carving. Each of the artists work with their own handmade tools. Which made me wonder, are true artisans also expert tool makers?
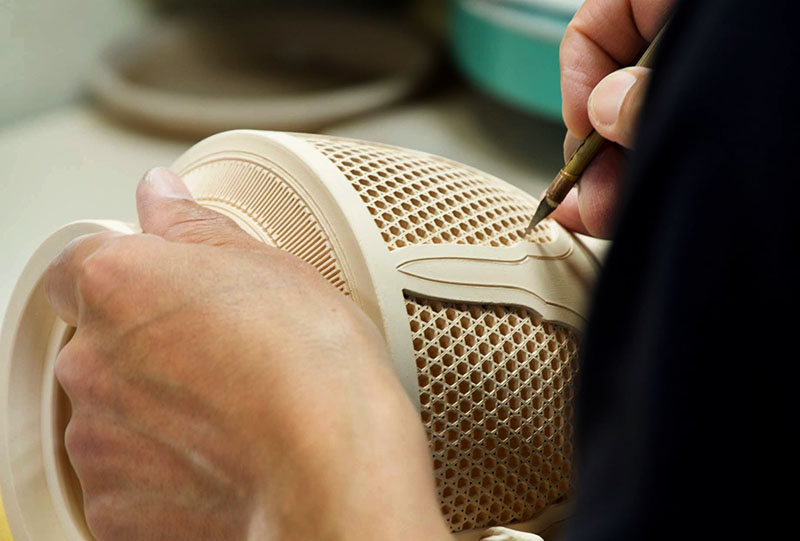
Decorating the vessel with carved-openwork
We also observed the painting process. Painters were busy decorating mice figurines, the Chinese zodiac animal of 2020.
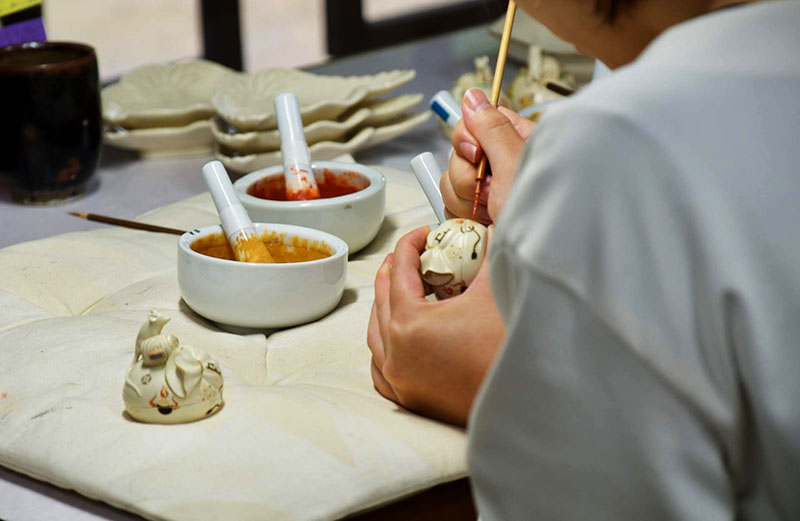
Drawing fine lines
The final stage of the production process involves applying glazes to the pottery, before firing. Interestingly, different glazes are used for white and black Satsuma ware.
Before the firing stage, the whitish glaze applied to the white Satsuma pieces gives the surface a matte texture. However, the firing yields a transparent finish that enhances the whiteness of the clay.
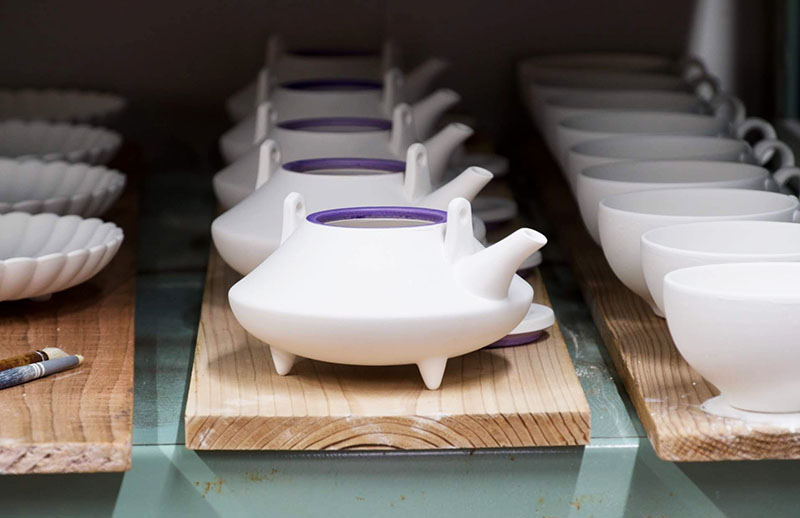
White Satsuma's matte texture before firing
The glaze applied to black Satsuma adds a terracotta-like color, which is caused by the glaze's iron content. The surface changes into a dark black or brownish hue after firing.
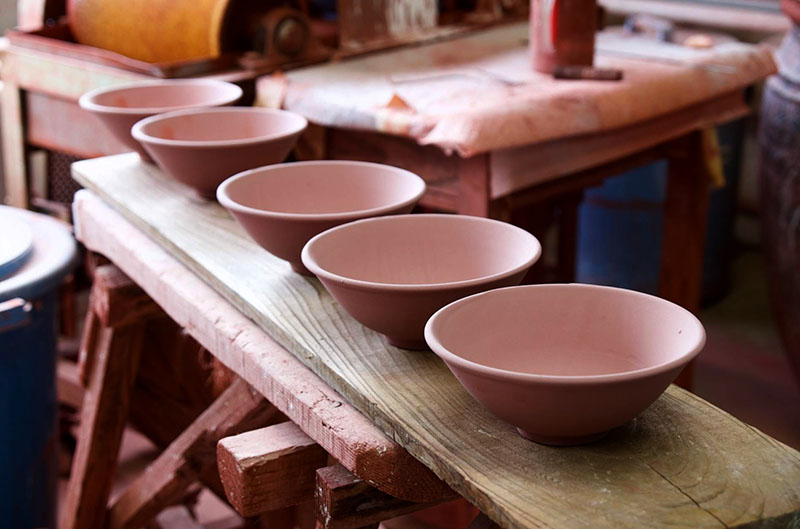
The reddish glaze of black Satsuma
Once the glaze is applied, the pottery is ready for firing. The temperature is set above 12-hundred degrees, making the entire room very warm.
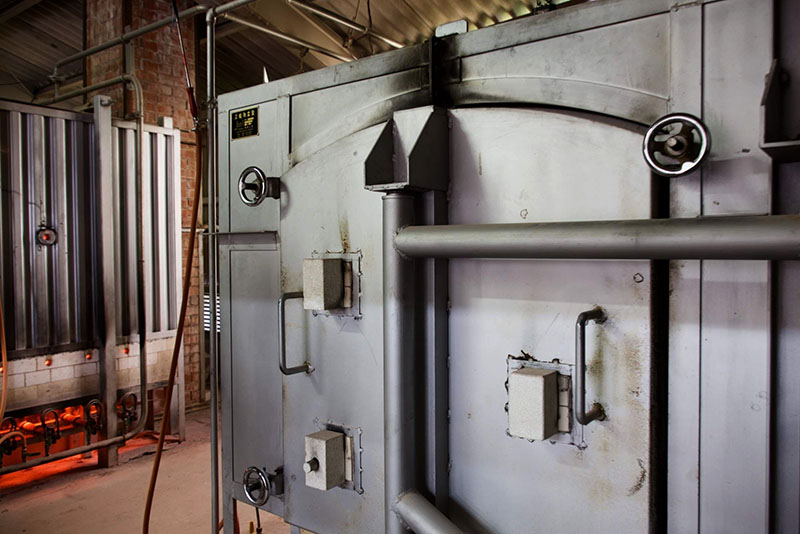
The sweltering kiln
Personal favorites
There are many different types of Satsuma ceramics. Here are my three favorites pieces at the Chin-ju-kan museum.
■1. Black Satsuma cup
Black Satsuma cup
This cup was not exactly eye-catching, yet it had an impressive deep black glaze that almost appeared brown or green. I prefer the Black Satsuma ware, as it seems to have a more calming feel than the white pottery.
■2. White Satsuma incense burner
White Satsuma incense burner
This fascinating piece is decorated with delicate openwork and gold paints. It is hard to tell from the photo, but it has another beautifully carved incense burner inside.
■3. White Satsuma Kongo-rikishi (temple guardian) statues
White Satsuma guardian statues
It is hard to believe these beautiful ivory figures are earthenwares made from clay. I was awestruck -- a feeling perhaps shared by Europeans who cherished Satsuma ware for their intricate decorations.
Try Painting Satsuma Pottery in Miyama!
Visitors to Miyama can try their hands at the potter's wheel, or other various stages of the production process. All the necessary tools are available on the spot. These are wonderful opportunities for first time potters, or anyone hoping to learn more about Satsuma ware. We tried painting at Miyama Touyu-kan, a recreational site that runs workshops related to Satsuma ware.
Miyama To-you-kan runs workshops
We began the session by choosing a white Satsuma piece to work with. We had a wide range of options to choose from, such as tea cups, mugs, bowls and saucers.
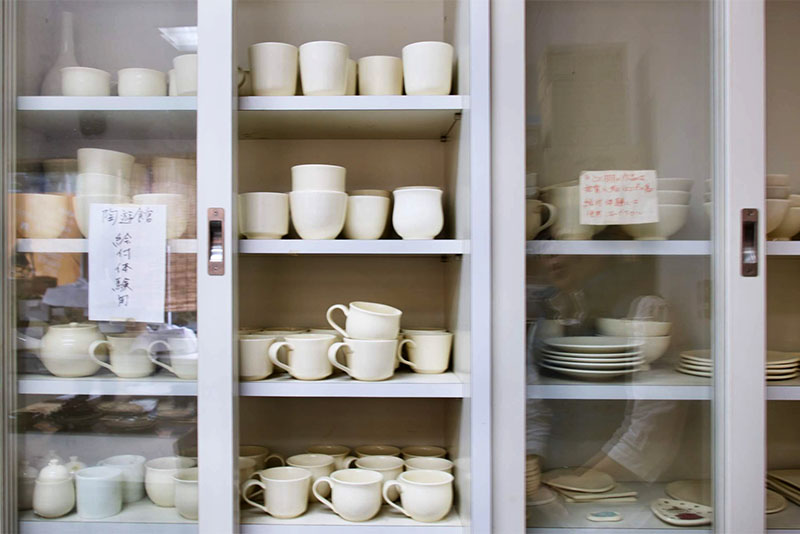
Many options
We were allowed to draw freehand, or use helpful tools. Fret not if you consider yourself artistically challenged! Sketching is a breeze if you use the cut-out templates drawn on stencil paper. All you have to do is rub the drawings and transfer them onto the pottery.
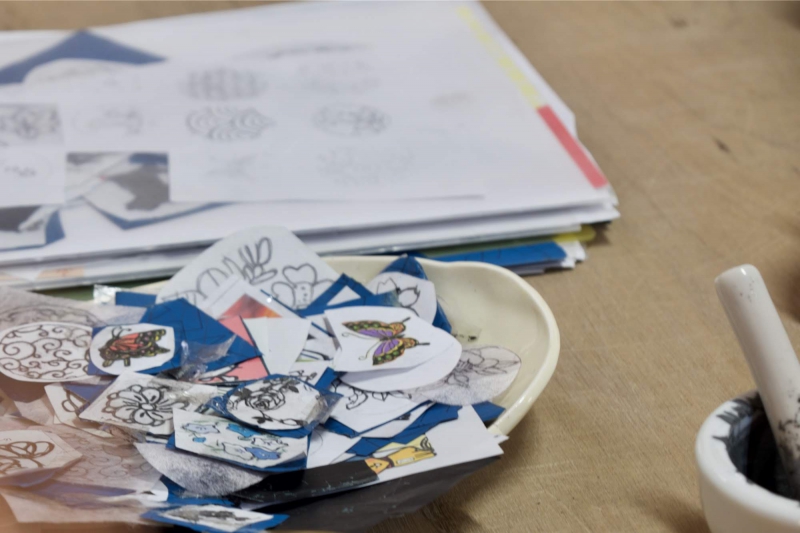
Cut-out drawings on carbon stencil paper
White Satsuma ceramics are decorated with pigments, which change color after firing. We used the color chart to determine our colors.
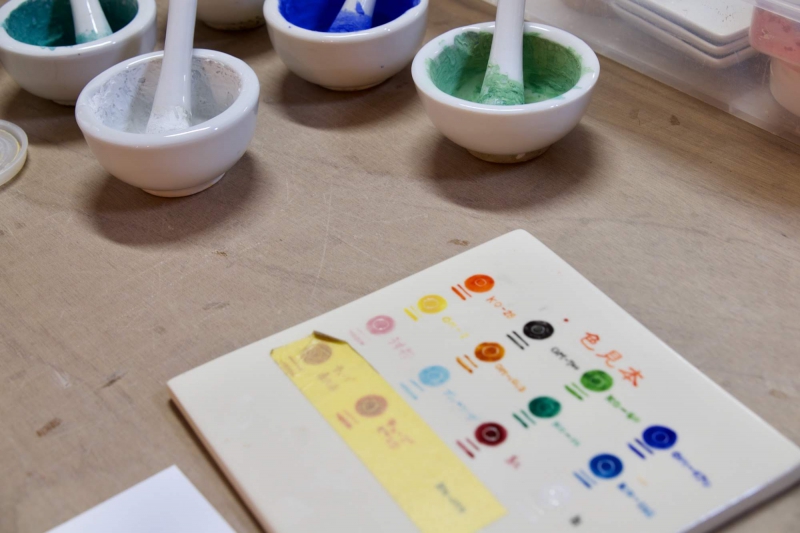
We used the color samples to decide our paints
After we sketched and decided our paint colors, we were ready to decorate. The feeling of the process is not so much “painting”, as it is “placing” the colors. The secret to drawing fine lines was to hold the brush vertically and apply gentle strokes.
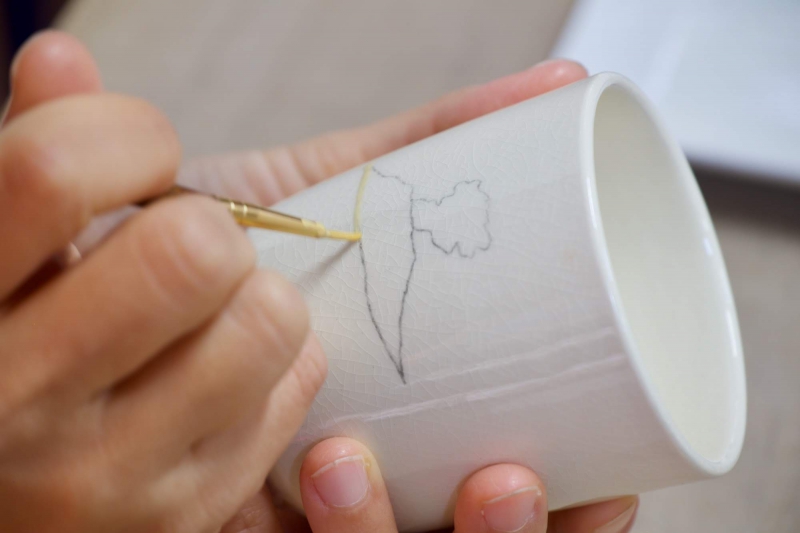
Applying colors
Coloring the larger areas was even harder. It was especially difficult trying paint a smooth surface. In this step, it is important to choose the right brush size. Once we were done decorating, we still had untouched space. We added some patterns.
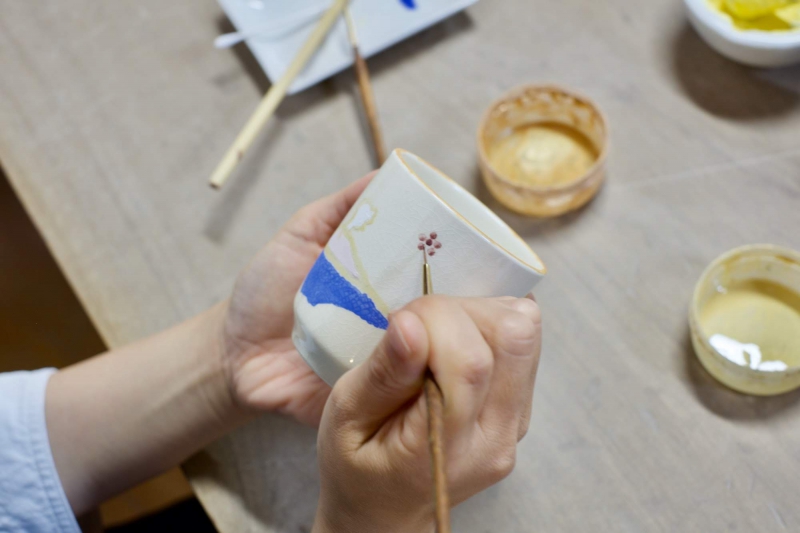
Adding fine details
We finished off our pieces by adding our signatures. The workshop ran for about 50 minutes, but it felt much shorter. Avoid spending too much time on sketching and choosing paints. Otherwise, you will have little time to focus on decorating. Our pieces were fired at the kiln and delivered to us about a month later.
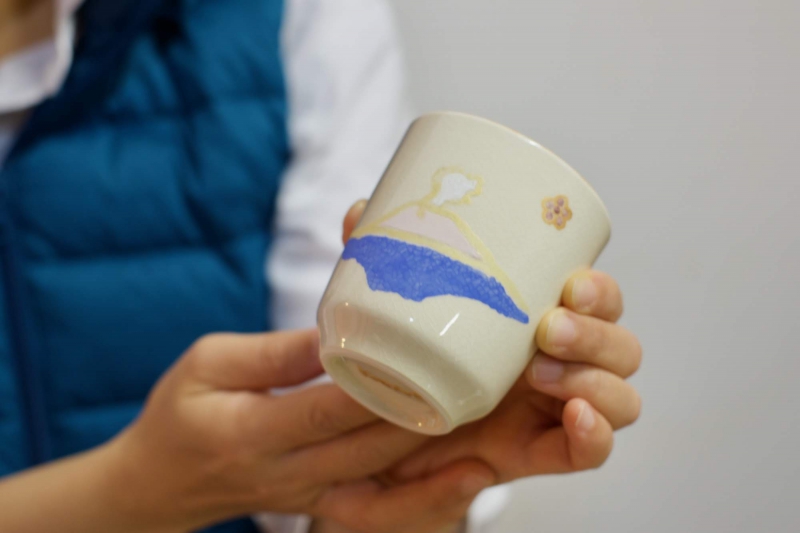
After firing, the piece was shipped to us a month later
Immerse yourself in the World of Satsuma Pottery
Satsuma ceramics are awe-inspiring pieces that boast a special place in the history of Japanese art. Visit Miyama pottery village to witness how potters have plied their craft for centuries, and be sure to have a try at making your own special Satsuma piece.