Satsuma Kiriko is the sparking cut glassware that hails from the region of its namesake. In Satsuma, or present day Kagoshima in southern Japan, the art of glassmaking briefly flourished in the late 19th century, only to disappear a few decades later.
The lost art was brought back to life more than a century later by modern-day artisans.
For this article, we visited the glassmaking studio that led efforts to revive Satsuma Kiriko cut glass, and took a closer look at the passion driving its artisans.
Satsuma Kiriko -- the rise, fall and ressurection of a legendary craft
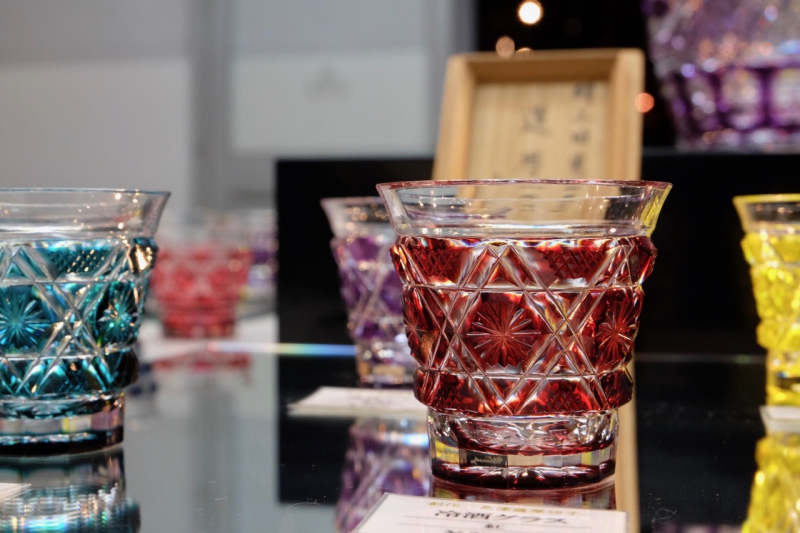
Beautiful yet practical glassware
Satsuma Kiriko is made by layering colored glass over clear glass, and cutting patterns into the surface. The detailed patterns reflect light, producing a gem-like sparkle. The traditional glassware is not only a gorgeous art piece but also valued for its practical applications.
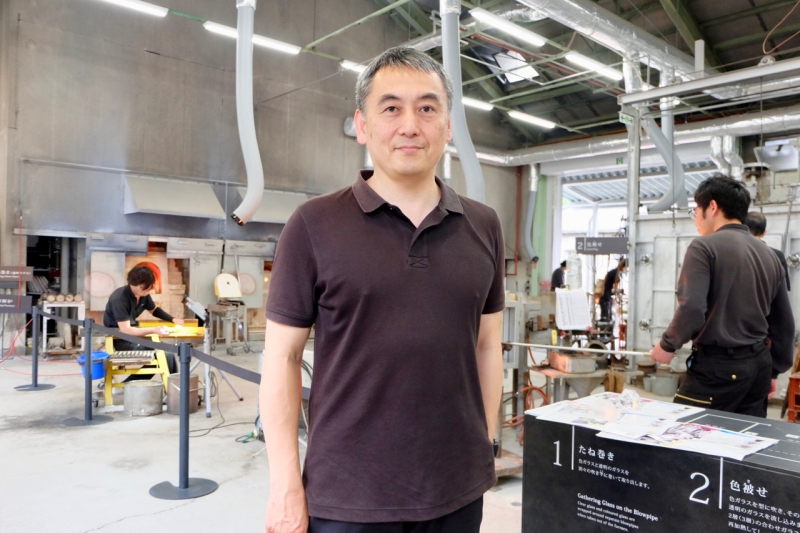
Our guide: Mr Hitoshi Arima of Satsuma Glass Crafts
Although Satsuma Kiriko is one of Kagoshima Prefecture's traditional crafts, there are only five producers. Satsuma Glass Crafts is one of the only two companies involved in the entire production process, from glassblowing to cutting and polishing.
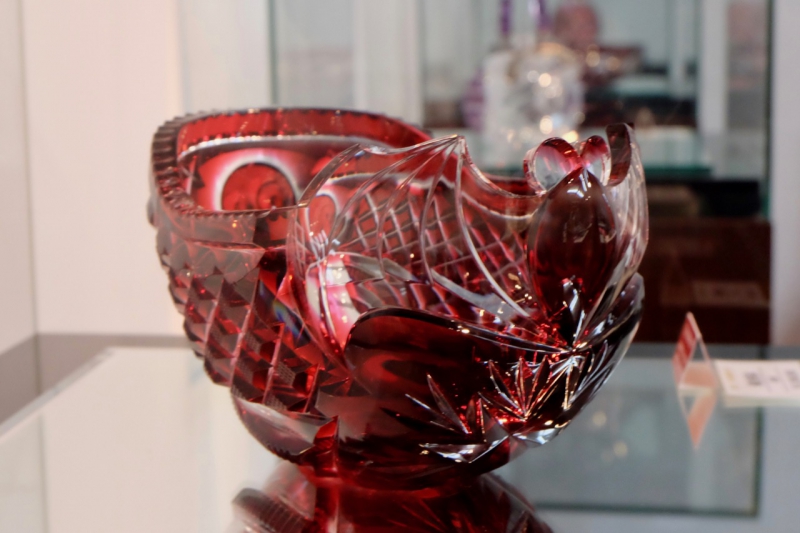
Reproduced bowl engraved with a ying-yang pattern and a bat spreading its wings
Satsuma Kiriko was first created around 1840, during the last few years of the Edo Shogunate. At that time, British and other western powers were expanding their foothold in Asia. In response, the ruler of the powerful Satsuma Clan, Shimadzu Nariakira, launched a series of projects with the aim of modernizing Japan and boosting its industry.
A distinctive feature of Satsuma Kiriko is its gradation of colors, which are created by layering colored and colorless glass to make deep incisions on the glass surface. The sparkling glassware was a cutting edge piece for that era and was offered as gifts to other feudal warlords.
Restoring the lost traditional art
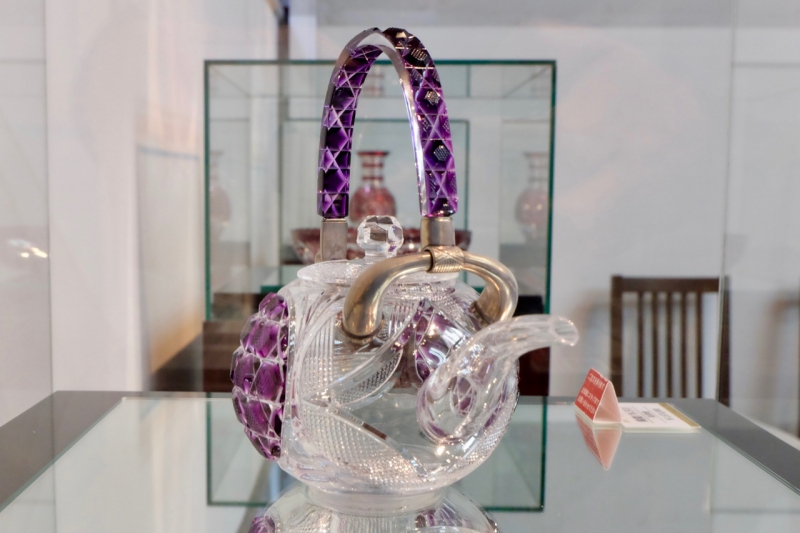
Special gradation techniques are applied to create this reproduced Chirori sake server
Nariakira's projects began making an impact on Japan's modernization, but they were significantly scaled down after the ruler's death in 1860. Satsuma cut glass techniques eventually disappeared due to the discontinuation of production during the civil war in 1877.
It took more than a century for Satsuma Kiriko to come back to life. In 1985, a company linked to Nariakira -- Shimadzu Limited -- founded Satsuma Glass Crafts in the Iso district of Kagoshima, which was once the center of Satsuma's industrialization programs.
The project to restore Satsuma Kiriko faced many hurdles. To begin with, there were only a few remaining pieces of the original Satsuma Kiriko cut glass. Artisans scrutinized them and poured through old manuscripts in search for more details. At times, they only had a single photo to determine the shape, design and colors of a certain piece.
However, the young artisans were driven by passion and perseverance. After much trial and error, they developed an original cutting technique and recreated the traditional colors of crimson, indigo, purple, green, yellow and copper red.
More than a century after its abrupt ending, Satsuma Kiriko was back for good.
New techniques, new applications
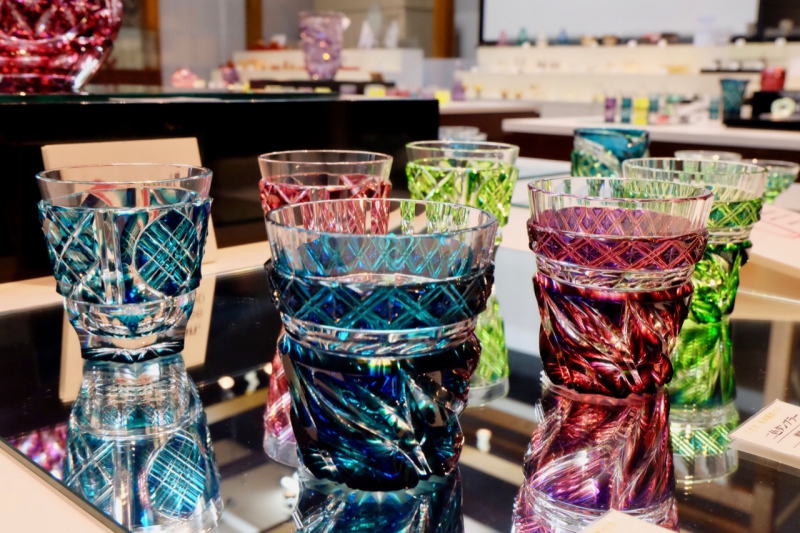
Sake-ware featuring new layering technique
In addition to reviving traditional techniques, Satsuma Glass Crafts also developed new methods, such as the layering of two colors over a colorless glass. The "nishoku-gise" technique adds further depth to Satsuma Kiriko's color gradations. Such cutting edge techniques have taken Satsuma Kiriko glassware to new heights.
The difference between Satuma Kiriko and Edo Kiriko
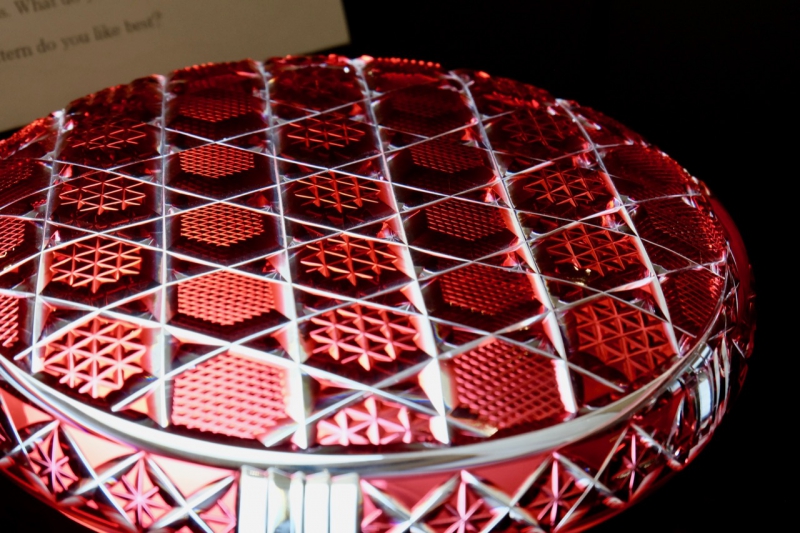
Satsuma Kiriko's distincitive color gradations are created by deep incisions
Satsuma Kiriko is similar to Tokyo's traditional cut glass called Edo Kiriko. Edo is the old name for Tokyo. The production of Edo Kiriko has continued without interruption since 1834 thanks to techniques fully established during the Meiji Era.
Both versions represent Japanese glass work, but their main difference is the cutting method. Edo Kiriko traditionally applies sharp incisions to the glass surface, while Satsuma Kiriko glass is cut at various angles that result in bold engravings.
Both glasswares are appealing, but in different ways. Edo Kiriko is delicately shaped with clear patterns. when you hold a Satsuma Kiriko piece, you'll notice its subtle gradations of color and its bold, dynamic feel created by the uneven surface.
At a glance, it is hard to differentiate between the two glasswares.
It is only when you actually hold them in your hands and examine the thickness of the glass and depth of the incisions, that you will begin to notice their unique qualities.
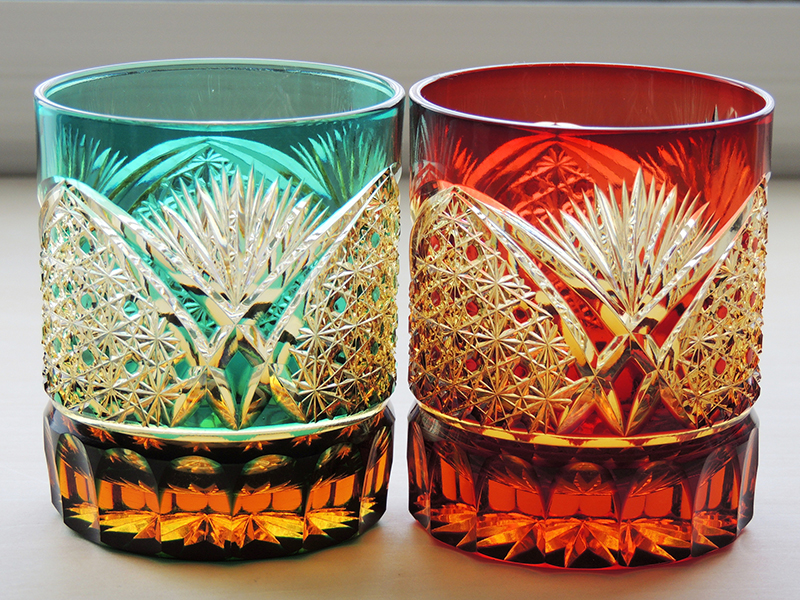
Edo Kiriko's thinly colored glass with delicate engravings
Edo Kiriko is also slightly different from Satsuma Kiriko in terms of ingredients and applications. Edo Kiriko is made from the same crystal glass as its Satsuma counterpart but soda-lime glass is also used as a component. Also, Edo Kiriko uses a variety of cutting patterns, which results in a wide range of prices. Small sake cups can fetch prices anywhere between five-thousand yen to almost 100-thousand yen depending on the patterns.
An artisan's take on the appeal of Satsuma Kiriko
Many artisans were involved in the project to revive the long lost art of Satsuma Kiriko. We spoke to one of them, Mr Yuichiro Matsubayashi, who works at Satsuma Glass Crafts.
Interview with glass artisan
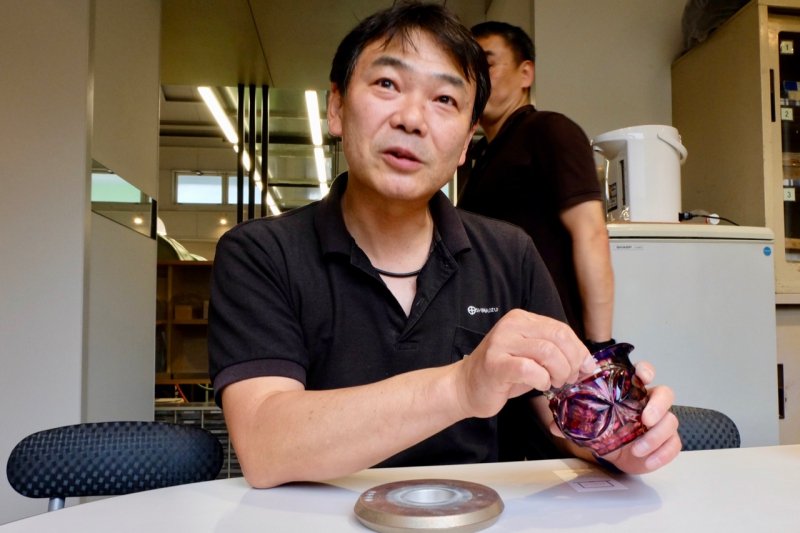
Mr Yuichiro Matsubayashi is one of the earliest members of the Satsuma Kiriko revival project
Mr Matsubayashi has been creating Satsuma Kiriko cut glass for 33 years. He used a spinning wheel to explain the production process and shared stories about the ups and downs regarding Satsuma Kiriko glassmaking.
ーーTo start, could you please briefly go over the Satsuma Kiriko production process?
The process is largely divided into molding and cutting. The first stage involves blending and melting the elements to make colorless and colored glass. The melted glass is applied to a bar that is used to blow a layer of colorless glass inside the colored glass. The raw glass is blown into metal and wooden moulds and shaped into a vessel. After letting that cool for sixteen hours, the glass is ready for cutting.
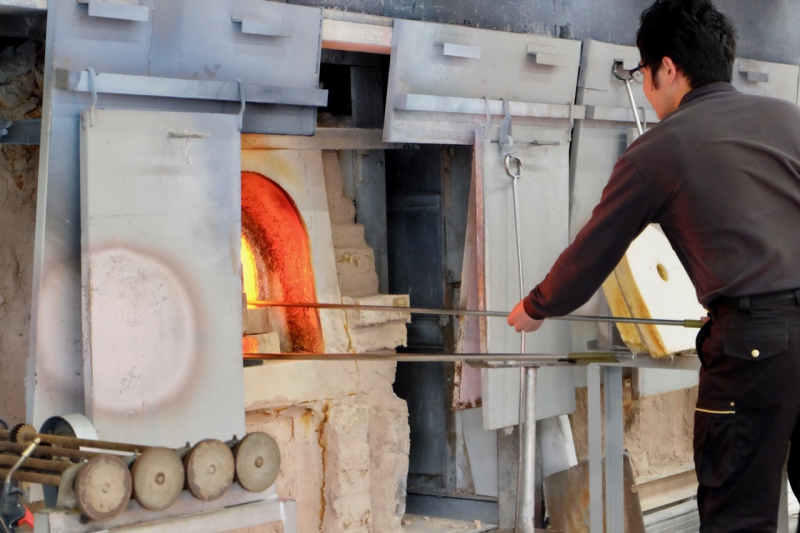
tanemaki: the process of wrapping glass around a bar inside a furnace
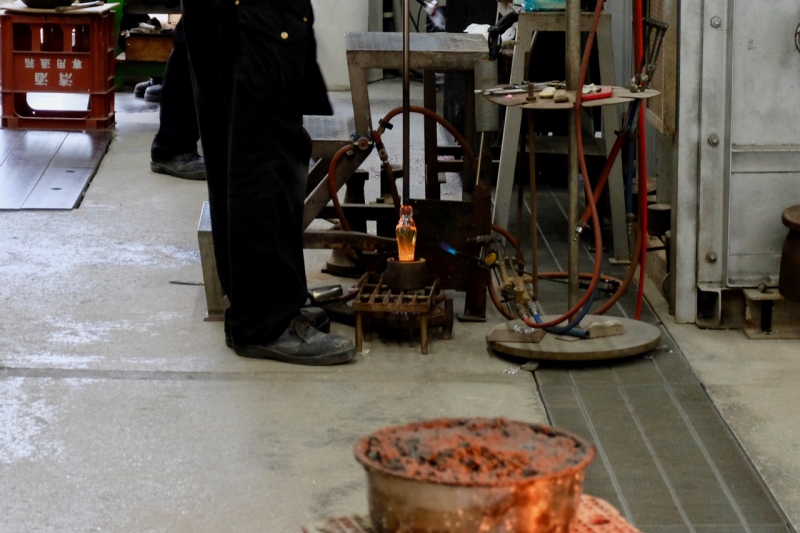
irokise: laying clear glass with colored glass
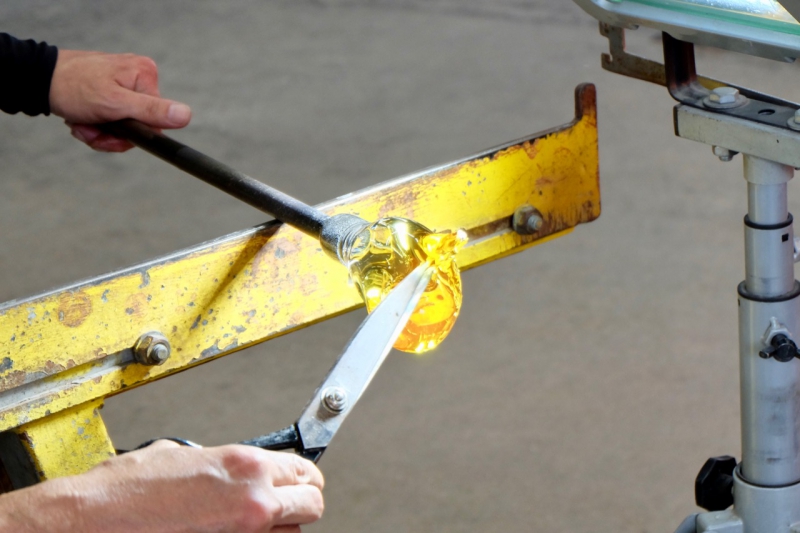
Removing impurities and bubbles by hand
The cutting begins with a process known as atari, or the etching of lines on the glass surface. The next step is arakezuri, or carving into the glass with a spinning wheel embedded with industrial-grade diamonds. Next, we carve the finer details of the pattern. After that, the glass surface and lines are polished with wooden disks and brushes. The last process involves polishing with a cloth-covered wheel to make the glass shine.
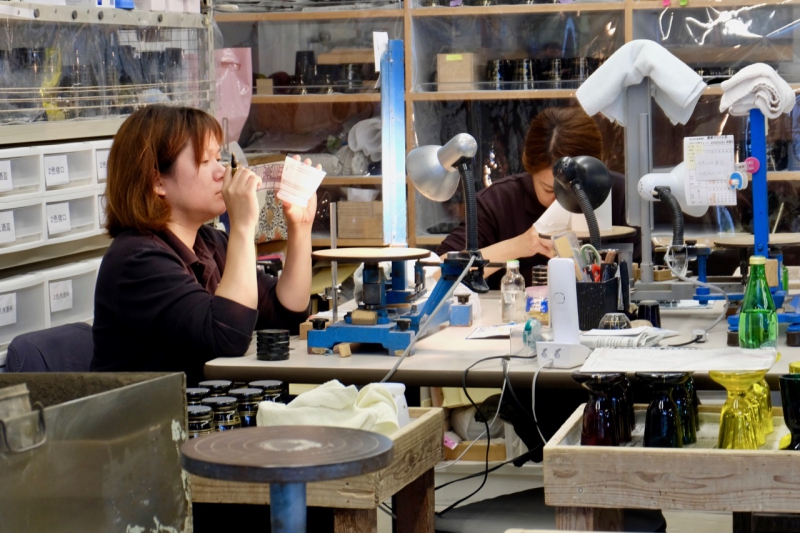
atari -- etching the guidelines for carving
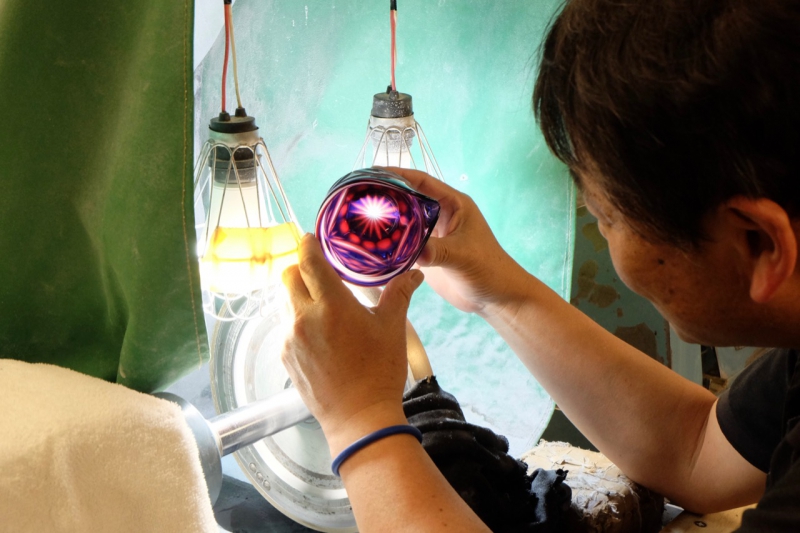
arakezuri -- cutting the glass surface with a spinning wheel embedded with diamonds
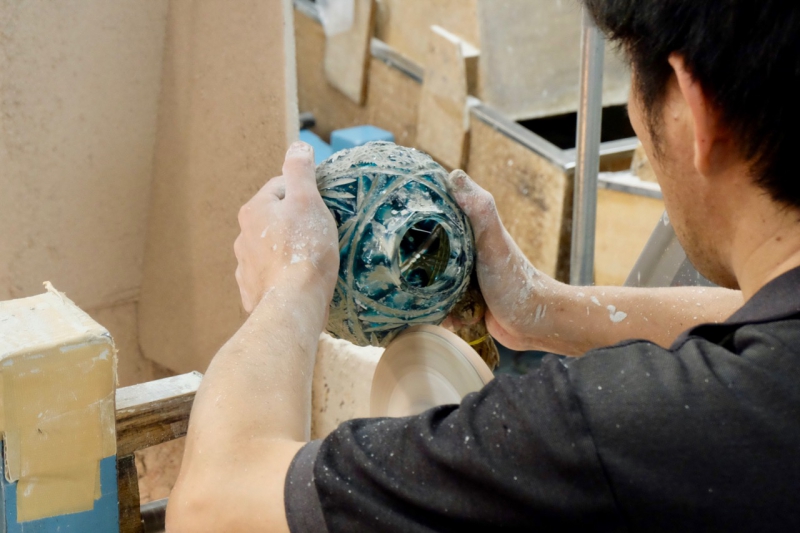
mokuban-migaki -- the process of smoothing the rough edges with a wooden wheel
ーー Which areas of Satsuma Kiriko glassmaking do you find particularly challenging?
Satsuma Kiriko is special because of its intricate engravings. There are three areas in cutting that require special attention. First, the lines. They need to be accurate. The second point is getting the angles right. And the last point is the depth of the cut. Although we are experts in this field, artisans are humans too -- it can be challenging to keep all this in mind while working.
So here's the solution -- We need to fully acquire two of these three skills and be able to perform them effortlessly. That allows us to stay focused on the remaining process.
It takes time to learn these skills. It'll probably take at least 10 years of training
to master glass cutting.
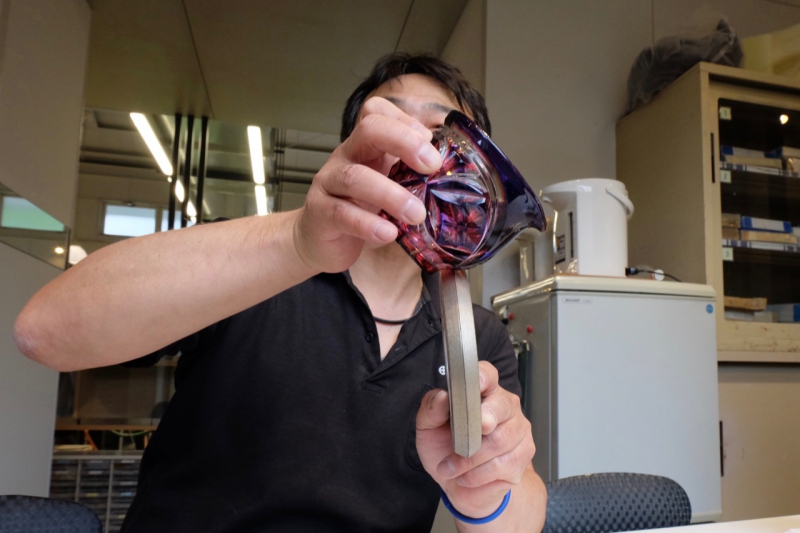
It takes time to master the skill of engraving
ーー Tell us the appeal of Satsuma Kiriko.
Firstly, it's visually pleasing. The patterns of Satsuma Kiriko are cut at various angles and depths, which creates a gem-like sparkle when exposed to light. The bokashi gradation technique also makes Satsuma Kiriko glassware special.
Satsuma Kiriko has a pleasant texture too. The surface is bumpy but it's shaped to fit in your hands. It has a unique feel.
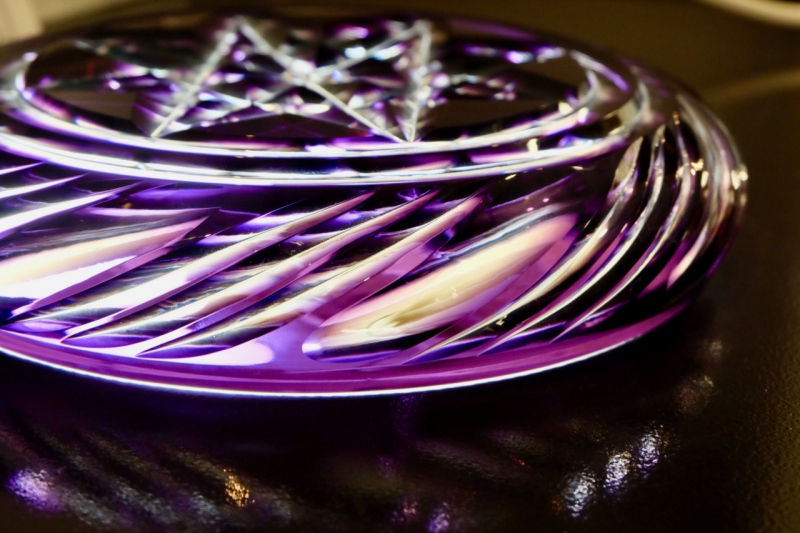
A creation of skilled craftsmanship
Glassware is cold and hard but Satsuma Kiriko glassware has a warm, gentle appearance and feel that makes it special.
ーー Let us end this interview with a few words for anyone interested in Satsuma Kiriko cut glass.
One of the distinguishing features of Satsuma Kiriko is its delicate engravings. The engraving process is similar to a gamble, even for skilled glassmakers. I hope more people get a chance to appreciate this art first hand. Enjoy the beautiful incisions, patterns and texture as you hold Satsuma Kiriko in your hands.
See Satsuma Kiriko in its modern glory
Satsuma Kiriko cut glassware once disappeared but restored its shine a century later. Observing the artisans at work and actually touching the cut glass made it easier to understand its special charm.
Satsuma Glass Crafts welcomes visitors free of charge. Photography is allowed (no flash), so make time to stop by and learn about the special art of glassmaking.