There are traditional crafts with unique history and locality all over Japan. "Lacquer “Wajima-nuri” is one of them, which is produced in Wajima City, Ishikawa Prefecture, Hokuriku region. Wajima-nuri is now a traditional craft which attracts not only Japanese people but also people from all over the world.
With the cooperation with “Wajima Museum of Urushi art”, this article leads you to the exploration of the attraction of wajima-nuri with the history, the feature, and how it is produced.
What kind of craft is “Wajima-nuri”?
The lacquer which uses powder of Wajima ground
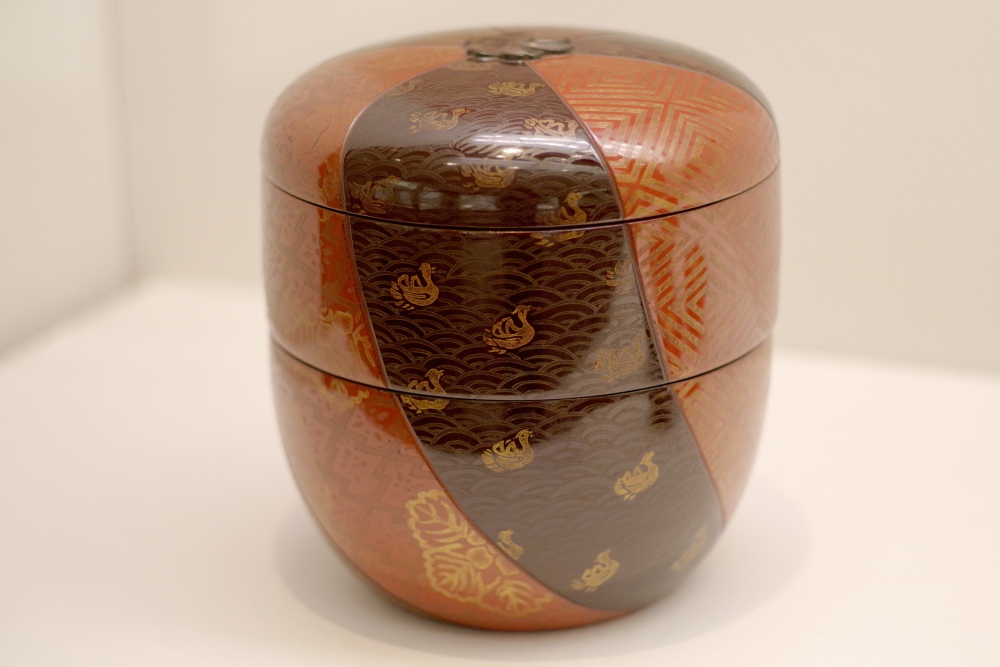
Wajima-nuri
“Wajima-nuri” is a luxury lacquer which is produced in Wajima city, Ishikawa Prefecture. It is not only strong and tough but also artistically beautiful. Even if it is broken, it can be fixed, so it is a masterpiece you can use throughout your life.
The feature of wajima-nuri is the usage of “diatomaceous earth” for groundwork.
The diatomaceous earth is used a lot for as wall materials of houses because of its quick absorption and quick dry. How much do you know about the material?
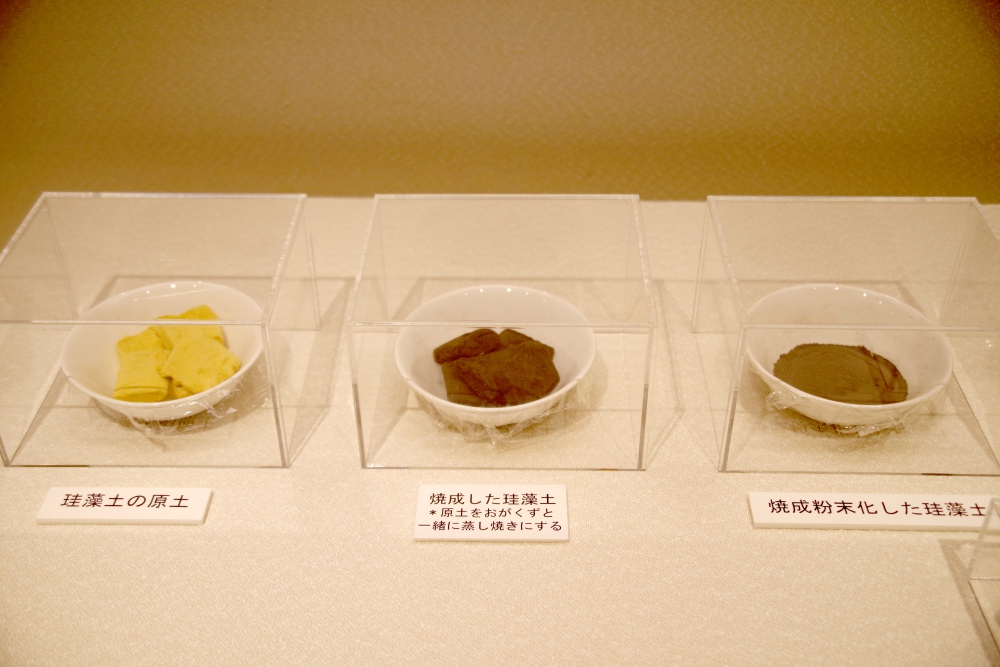
The diatomaceous earth used for wajima-nuri
The diatomaceous earth is a stratum formed by petrifaction of phytoplankton and deposited diatom shells. The multiparous holes instantly absorb liquid. When absorbed liquid reaches certain quantity, it discharges the liquid with spontaneous respiration, so it has a humidity control effect.
The diatomaceous earth collected in Noto Peninsula is burned into powder, which is what is used for wajima-nuri usage. It is called “Wajima ground powder (Zinoko)” by local people. The biggest feature of wajima-nuri is the strong groundwork. The little holes of the diatomaceous earth absorb lacquer liquid during the rough coat process.
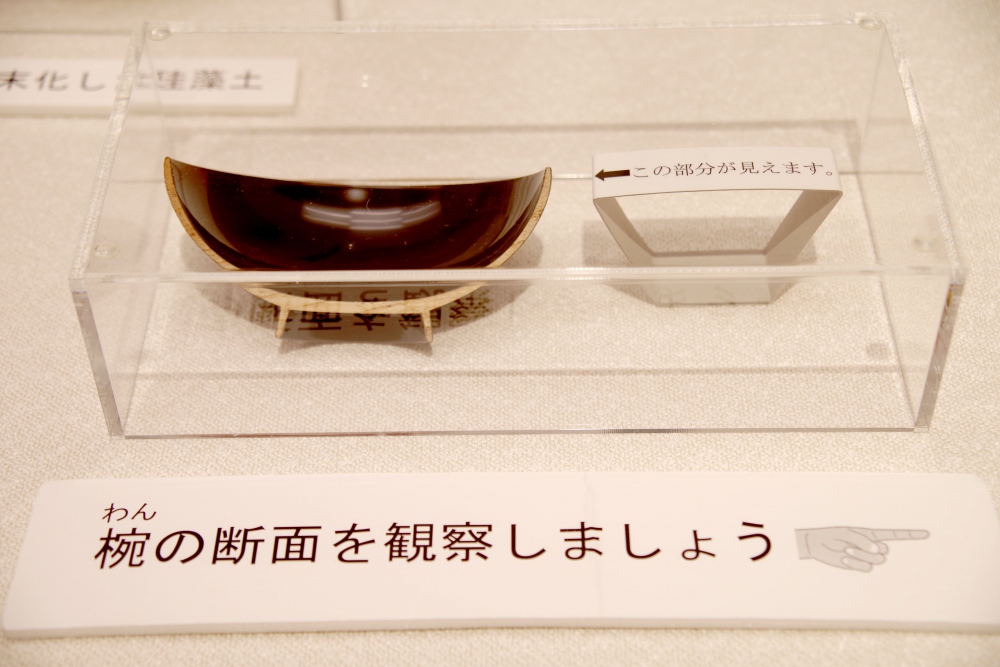
Section of wajima-nuri
When wajima-nuri is cut, you can see the base area decorated in the wooden basis. Lacquer wares excavated from the excavation site can be distinguished as wajima-nuri by the section.
Also, the section (the ground part) is so thick, which shows how tough wajima-nuri is.
Wajima-nuri started production in the Edo period
It is considered that lacquer wares have been produced in Wajima since ancient time, but wajima-nuri dates back to the 17th century.
As Wajima was an important port of call of the Japan Sea route, general producers of wajima-nuri called Nushiya promoted wajima-nuri all over Japan.
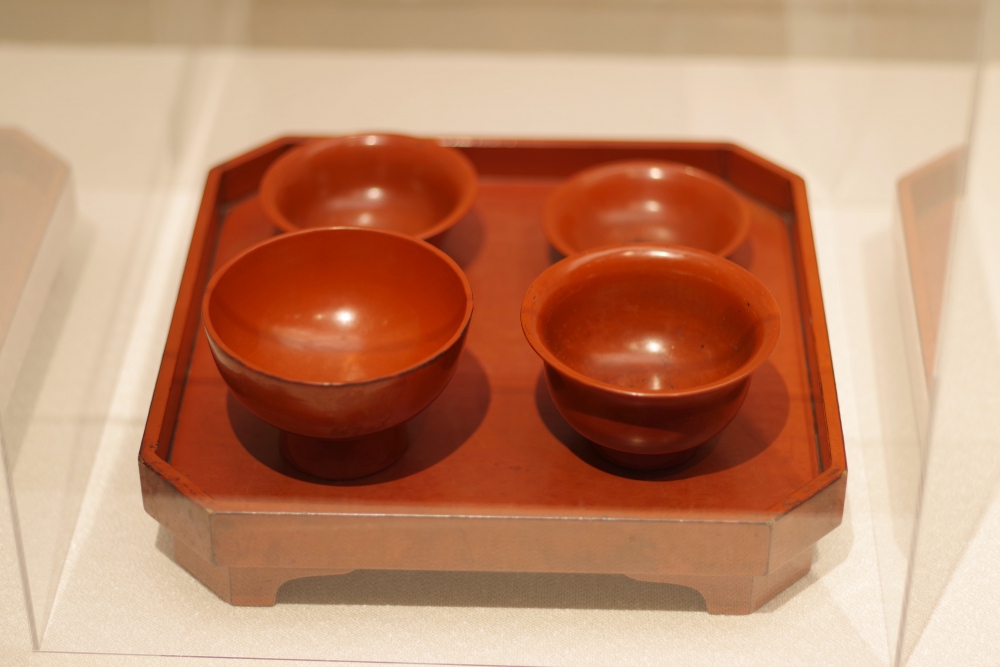
A bowl made in 1669
The bowls made in 1669 are displayed at the Wajima Museum of Urushi Art.
Although the bowls were made 350 years ago, the state of preservation is so good that you can use them without any problems. They must have been used as tableware on celebrative occasions. You can see how skillful wajima-nuri craftsmen are.
During this time, wealthy farmer families and wealthy merchants collected lacquer ware as a high-status thing. Having strong and well painted wajima-nuri became a symbol of richness and everybody admired it.
Plus, although Wajima is inconvenient to go to by land, it is famous for Kado and Sado. Why is that?
That is because Nushiya needed to be a person with wide interests when they recommended wajima-nuri to wealthy farmer families and wealthy merchants. When they came back to Wajima, they spread the culture of Kado and Sado.
The feature that the culture was spread through lacquerware is an important element in the history of wajima-nuri.
How long does it take to complete wajima-nuri?
It takes 100 process for completion.
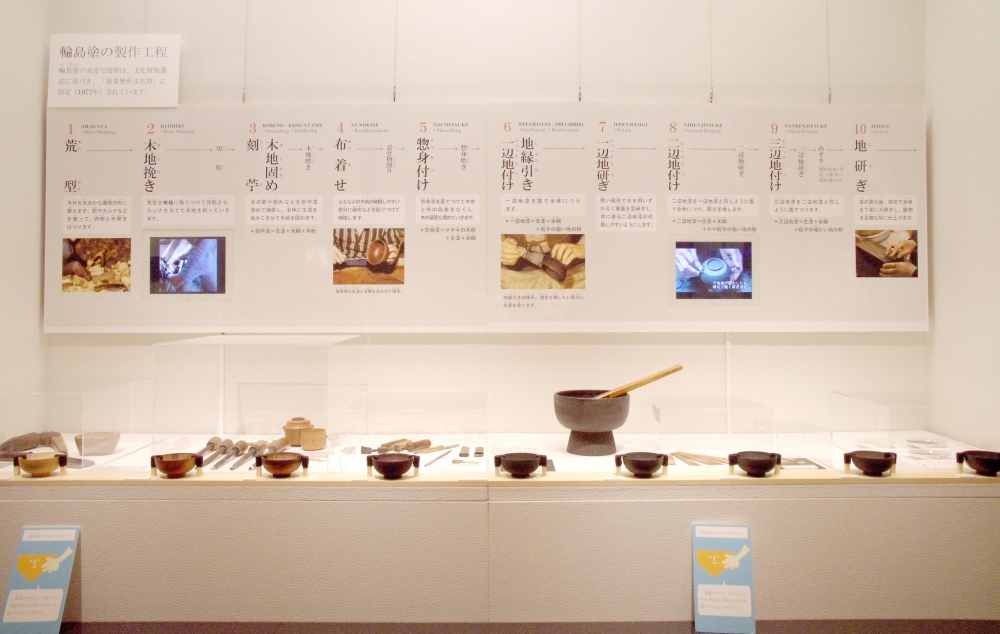
The production process of wajima-nuri introduced at Wajima Museum of Urushi art
The remarkable point of wajima-nuri is that it has many processes to complete. In some cases, it has over 100 processes to complete one lacquer.
Since a long time ago, each process was dealt with by specific craftsman to be able to respond quickly to a large number of orders, which was organized and sold by Nushiya.
Nushiya oversaw planning, development and production and organized professional craftsmen who were in charge of each process. They were also itinerant traders who sold wajima-nuri all over Japan. Wajima-nuri became what it is thanks to Nushiya’s effort.
You can experience the simplified production process with the touchable sample production tools at Wajima Museum of Urushi Art.
This time, we will introduce the 3 key processes to make strong and beautiful wajima-nuri.
Point 1: Wooden base and groundwork
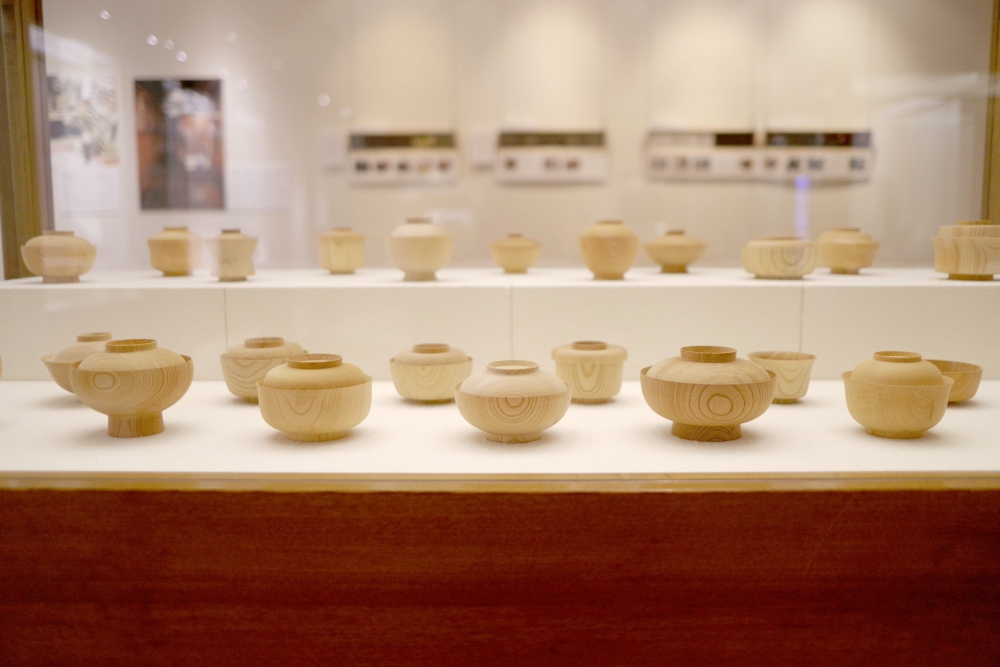
The wooden base for the lacquer of bowl for wajima-nuri
Making wooden base means to make the shape of a bowl. In case of wooden base for bowl, after taking rough impression of raw wood which turns into wooden base, it is smoke dried and naturally dried for a year. Smoking dry makes the edge of wooden base blackish and shaving makes the white and beautiful part appear. By taking a long time to dry the liquid inside the wood, deformation of the wood can be prevented, crack does not happen, and durability improves.
Different tree species and techniques are used depending on the use of bowls.
The ground base is invisible after completion, but it is a very important since it decides the toughness, which can be said as the biggest feature of wajima-nuri.
It is important to apply the ground lacquer evenly and to shave carefully.
Point 2: Coating
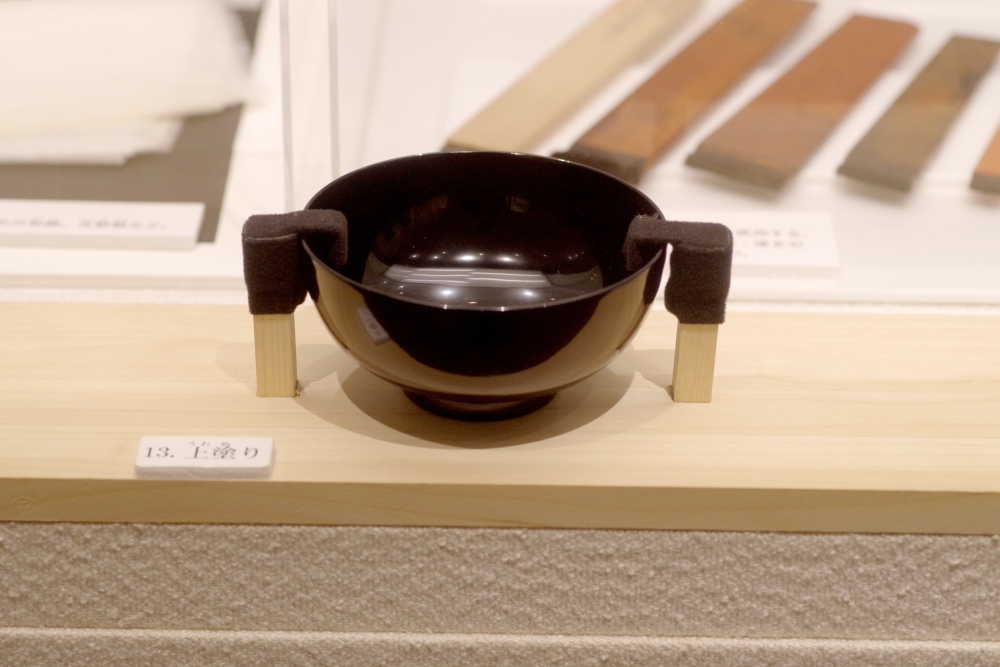
Black and glossy wajima-nuri with coating
In the last process called coating, lacquer is carefully applied to the bowl. Several kinds of brushes are used to apply filtered finest lacquer evenly so that the lacquer is not too thick or too thin. It is important to be careful not to get dust or dirt. This process is performed in the coating room where there is no dust or dirt and temperature remains the same. During solidification, the bowl is rotated so that the thickness of lacquer can be even.
Point 3: Pattern
■Gold-inlaid lacquerware
The process of gold-inlaid lacquerware
The decoration method, includes carving a pattern on the lacquered surface with “chinkinnomi”, rub in lacquere, and stick gold and silver foil. Various patters are made depending on the shape of chinkinnomi and how it is used for shaving.
■Gold lacquer
The process of mother-of-pear
It is called mother-of-pear because after drawing a pattern with lacquer, gold and silver powder is set before lacquer gets hard.
It is really difficult to draw a pattern with sticky lacquer liquid. Momentum of thin line should not be lost, and vast side of the brush should not leave the trace. Carefully planning is necessary with how to set gold and silver powder and the thickness of lacquer.
Through various processes, wajima-nuri is completed. The whole process is not performed by one person, each craftsman performs each job for effective production. Every Wajima-nuri work is one and only as it is made by craftsmen by hand.
It is considered as luxurious lacquer ware because of being such a detailed job.
Learn more about wajima-nuri at “Wajima Museum of Urushi art”
The only museum specializing in lacquer art in the world
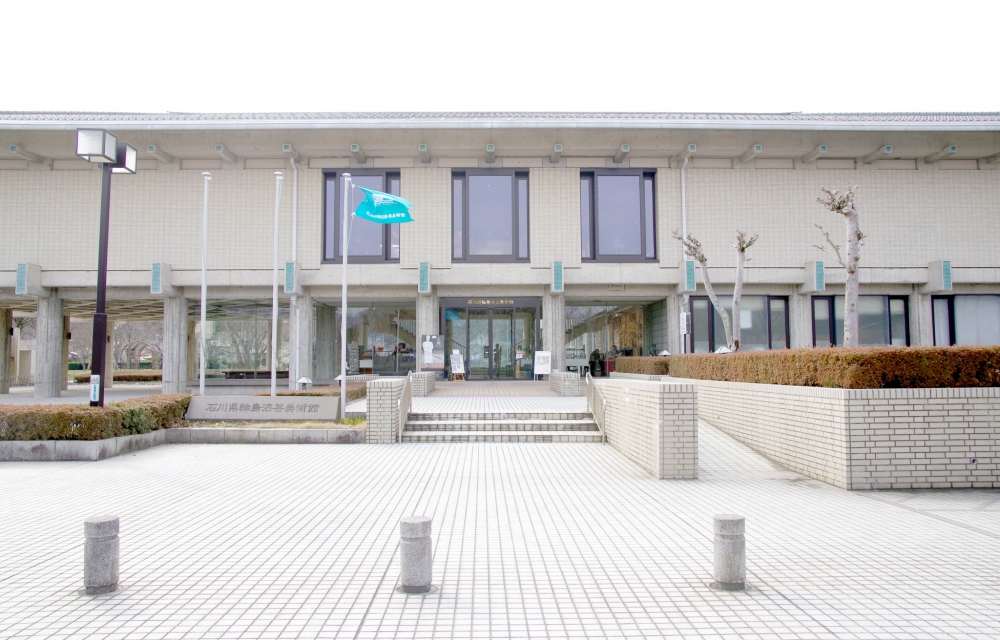
Appearance of Wajima Museum of Urushi art
Explore the history and the feature of wajima-nuri at “Wajima Museum of Urushi Art” located in Wajima city.
It is the only museum specializing in lacquer art in the world where all the rooms always show lacquer craft works. It opened to spread lacquer culture in 1991.
The unique building was modeled after log house style of Shosoin. Inside is spacious with the arcade.
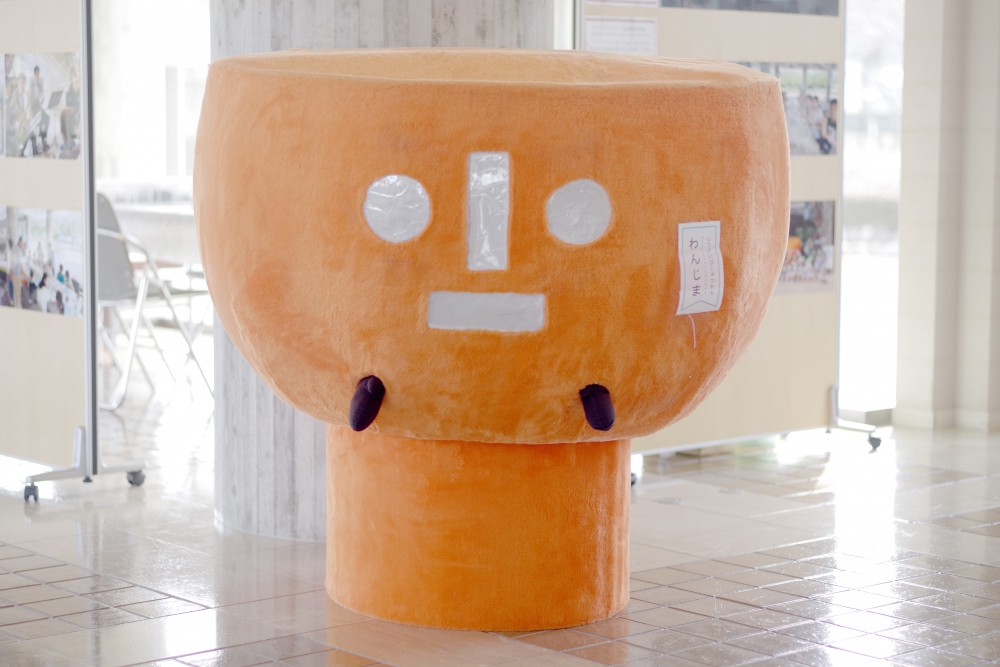
Mascot Wanjimakun
In the museum, official mascot of the museum "Wanjimakun" appears right in front of you. Wanjimakun used to be a sleeping bowl of wajima-nuri, and one day he could not move and help tell people how good wajima-nuri is.
He was born in the Edo period, aging 350 years old. Try taking a picture with him.
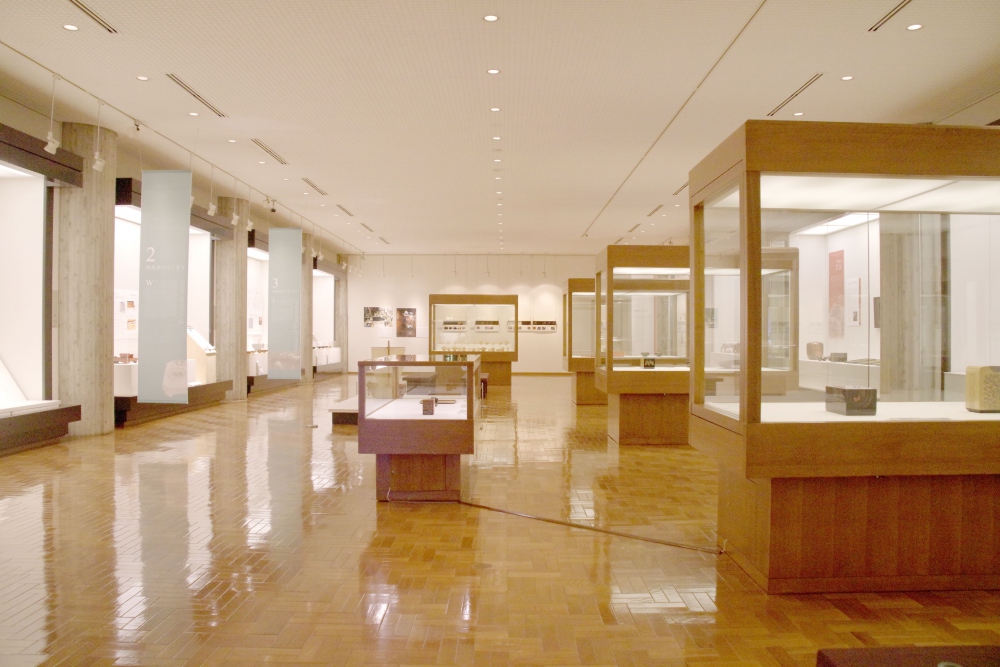
Exhibition room on the second floor of Urusi art museum
The exhibition room on the second floor of the museum shows various lacquer wares. Check out the panel to learn the history and the process.
Experience coloring chopsticks
In Urushi Art Museum, you can experience 3 kinds of things (- April 2019).
This time, we will introduce the experience of making gold-inlaid chopsticks using traditional technique of wajima-nuri.
①chose the chopstick with your favorite pattern
Choose chopsticks with pattern and color you want to make
Choose one among 4 chopsticks with different patterns. You can choose a color: within black or red. This time, we chose the combination of black chopsticks and wave pattern.
②Rub in alternative lacquer on the pattern
Apply alternative lacquer on pattern
After rubbing in synthetic resin coating obtained from lacquer on the pattern of chopsticks, wipe off the spilled part.
In this process, synthetic paint called alternative lacquer is used instead of real lacquer, so you do not have to worry about skin rash.
③Coloring
Put metal powder using a swab
Color chopsticks with 7 kinds of metal powders like blue, pink, and gold. Several colors can be used. You just need to slightly touch the chopsticks with a swab to color. We tried to use as many colors as possible.
④Wiping off
Wipe off metal powder
Wipe off the spilled metal powder carefully. Metal powder will stick to the pattern on the chopsticks.
⑤Completion
Completion of gold-inlaid chopsticks
We got a beautiful gradation with 6 colors of metal powder.
One stick was colored with one color. It is simple and beautiful.
Numerous patterns can be made in the combination of color of chopsticks, pattern, and metal powder. You can make the one and only chopsticks in the world. It will definitely add colors to you dining table.
◆Experience of making gold-inlaid chopsticks
・Fee: High school students or older: 1500 yen
・Junior high school students or older: 1100 yen
・Time required: about 20 min.
・Reservation: Appearance of Wajima Museum of Urushi art
Guide
The guide of the museum was the curator, Ayano Takatsu.
She got interested in wajima-nuri when she got attracted by glossy lacquer. Her major was art history in university. After that, she started to work at Wajima Museum of Urushi Art. While she was working at the museum for a year, there was a lot to learn and she felt the depth of Urusi art.
To those who visit Wajima, “There is a landscape in the original state like village forest and satoumi in Wajima. I want people to experience Furusato in Japan” she said. Wajima became popular as a sightseeing spot but come to experience the deep Japanese culture.
Information
〒928-0063 11,Shijukari, Mitomorimati, Wajima, Ishikawa Prefecture
0768-22-9788
9:00 AM - 5:00 PM (Last admission: 4:30 PM)
End of the year (December 29th - 31st), temporary holidays
Adult: 620 yen, High school students and University students: 310 yen, Elementary students and Junior high school students: 150 yen
“Wajima-nuri” made by the amazing technique of craftsman
Lacquer wares are used in many areas and families. The beautiful and tough wajima-nuri with diatomaceous earth has been a representative craft art in Wajima. At Wajima Museum of Urushi Art, you can not only find the attraction of traditional craftworks like wajima-nuri, but also experience making wajima-nuri. Why not come for a visit?