"Washi" is a traditional Japanese paper with a unique texture, feeling, and writing touch, which has long evolved and cherished to become one of Japan's iconic cultures.
However, not a lot of people know much about the history, way of making, and place of production of this Japanese invention.
This time, we visited a long-established Washi wholesaler in Nihombashi called "Ozu Washi".
Knowing thoroughly about this Japanese paper through its 360+ years of business experience since its foundation, we would like to dig into the attractions of the "Washi" from multiple angles.
At the same time, we will be introducing various Washi goods suitable for everyday use available in Ozu Washi.
Be prepared, since the more you learn about the appeals of the "Washi", the more your desire to embrace this traditional and cultural craftwork of Japan into your daily life will grow.
What is a “Washi”?
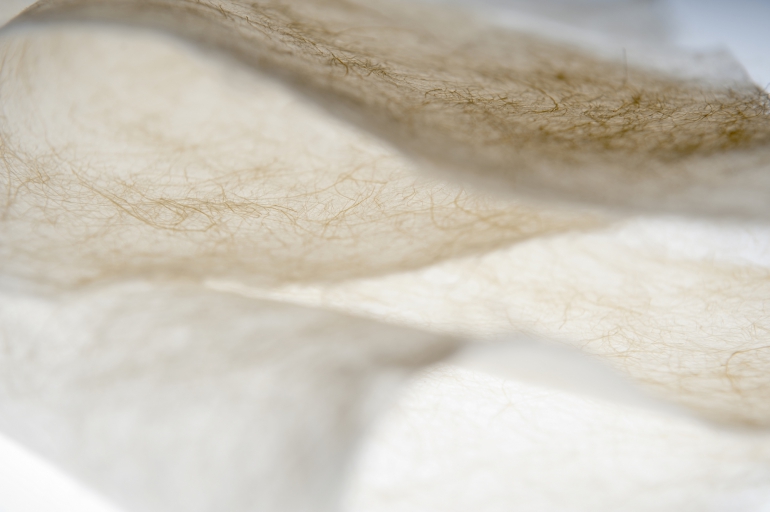
Washi has been deeply related to the lives of Japanese people
"Washi" has historically had a close relationship with Japanese culture.
To know more about its attractions, we've visited a long-established Washi manufacturer in Nihonbashi known as "Ozu Washi".
The Nihonbashi area of Tokyo is famous for being the center of many old stores and companies, and without exception, Ozu Washi also has a history of over 360 years since its foundation.
Although the hand-made papermaking workshop is especially popular, there are tons of interesting features to see as well, such as the various exhibits related to the history and making process of Washi being displayed throughout the 1st to 3rd floor.
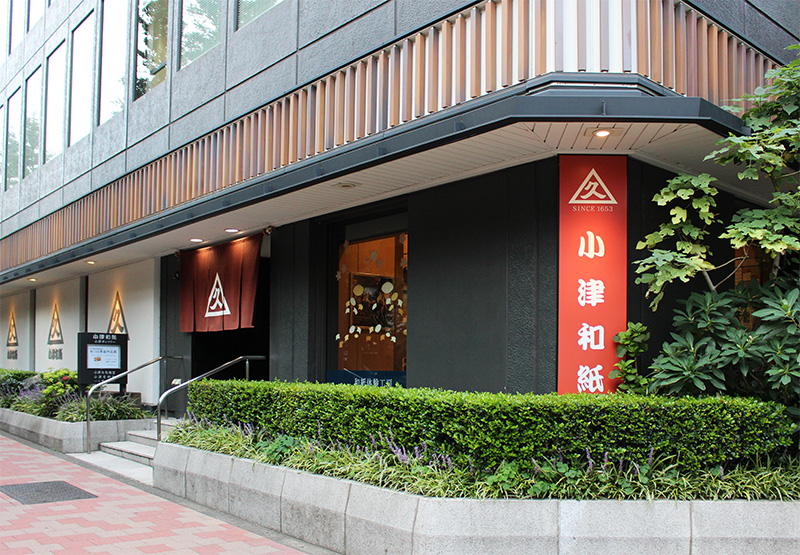
”Ozu Washi” is a long-established store founded in 1653
A postcard decoration experience is available at the 3rd floor, where you can participate freely without reservation.
Let’s begin our report on the actual visit to Ozu Washi.
In an attempt to discover the appeals of the Washi from various perspectives, we've met Mr. Takagi, the vice store manager of Ozu Washi.
The vice store manager, Mr. Kiyoshi Takagi
Firstly, there are currently two ways to make papers known as "Washi", either by hand or by machine.
Though it may sound obvious, this unique paper was all hand-made at the time of its invention.
The name "Washi" is a generic term given to distinguish it from the foreign "Western Paper", and this includes all paper made using the Japanese traditional paper making methods.
This time, we will mainly focus and dig into the attractions of the "Hand-made Washi", since it has a unique and long history of development, and this is the one we refer to as the traditional icon of Japan.
The development of Washi in Japan
The history of Ozu Washi along with various collections of Washi papers gathered across Japan are displayed at the 3rd floor. In addition to this, an exhibition called "The making of Washi; the process and the preservation storage" will provide detailed information about the Washi, starting from the introduction of the techniques involved in Washi making, and the history of how it came to pervade Japanese culture.
“The making process of Washi” corner displayed at the 3rd floor
<img src="https://s3-ap-northeast-1.amazonaws.com/thegate/2019/11/08/14/53/52/process-exhibition-room.JPG" alt="The inside of “The making process of Washi” />
You can learn about the history and making process of the Washi in Japan
Although there are various theories regarding the introduction of paper, it is stated in the "Nihon Shoki", which is the oldest chronicle of Japan, that it has first arrived during the Asuka era around A.D.610.
This is the era when empress Suiko held the reins of government, with Mr. Takagi adding, "At this time, all documents and records were written on a Mokkan(a strip of wood), but in order for the government to manage the enormous amount of family registers, they implemented paper as a substitute for the bulky Mokkan.".
When entering the Heian era, paper became mainstream among the nobles.
Many female writers of this period such as Murasaki Shikibu and Sei Shonagon, preferred writing on paper upon publishing numerous literary works.
It is said that the development of Washi started from this period, with paper being widely distributed among the aristocratic population.
The unique Japanese handmade technique of "Tesuki" was established at this time, allowing people to produce strong and thin Washi paper, which is a distinctive characteristic of Japanese traditional papers.
It became familiar not only for its main usage as a writing material, but it was also used in various interiors such as paper sliding doors (Shoji and Fusuma), paper-framed lamps, etc.
However, Washi was a luxury goods at that time, making it only affordable for the nobles, and by far, out of reach for the rest of the population.
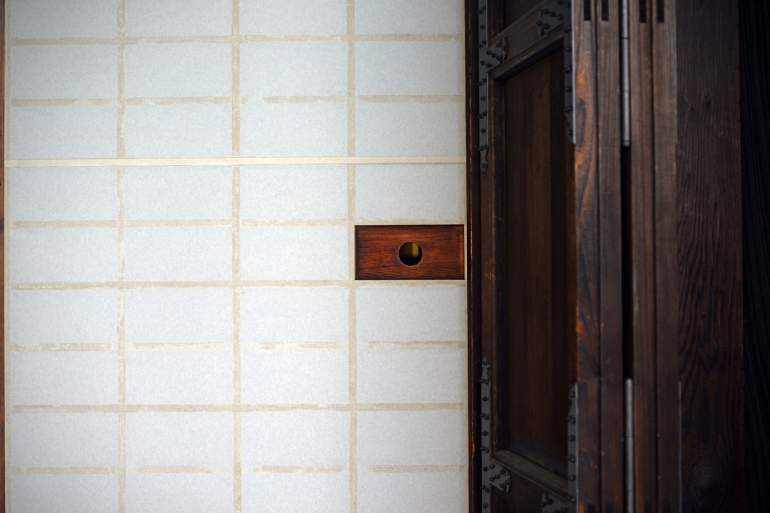
Washi has been used in interiors such as Shoji and Fusuma
After the end of the Heian era came the Kamakura era.
This is the period when Japan shifted to a Warrior Society, where the samurai rapidly gained power.
Here on, the samurais were the people to appreciate the luxury of Washi on behalf of the nobles.
They made use of the papers actively, as sending letters were their main tool of communication.
However, the paper was still unaffordable for the common people.
It was not until many years later for paper to become familiar to the majority of the population, which finally happened upon entering the Edo era.
During the Edo era, Washi was used in arts such as Ukiyo E paintings, along with realistic literature known as Ukiyo-zoshi and in textbooks used in schools of that time called Terakoya.
With this being said, publication and printing of books became extremely popular during this period, and you can say that this was the first time regular citizens were able to appreciate paper in their daily lives.
At last, the "Paper" culture successfully established an important position in Japan.
The traditions and makings of the "Hand-made Washi"
After being introduced to Japan during the Asuka era, the gradual development of the hand-made papermaking techniques lead the production of Washi to spread nationwide.
The greatest feature of the Washi comes from it being light weight and hard to tear.
To begin with, Washi is made from fibers of a tree bark, with the 3 most common trees being "Paper Mulberry", "Paper Bush", and "Diplomorpha sikokiana". These trees have long fibers which are entangled complicatedly with each other during the paper making process, producing the strong and liable to tear feature of Washi.
Shown left is the Paper Mulberry, and you can see that the length of the fibers are quite different compared to the Pulp seen in the right.
It is known to be so tough and light, that even garments such as "Paper Cloth(Shifu)" made from weaving paper-like a thread, and "Paper Clothing(Kamiko)" which is formed by kneading paper, are made from Washi. A wedding dress made from Washi is actually displayed in Ozu Washi for you to see.
A wedding dress made from Japanese paper is displayed at the corner of the 3rd floor exhibition corner A.
This dress was actually worn in the past, and you can feel the elegance and the tenderness coming from the Washi.
There's also a boutique handling wedding dress made from Mino Washi at Mino city in Gifu prefecture. Mino is known as "The town where the world rises", and is famous for its historical landscape and production of high quality Mino Washi.
How the handmade Washi is made.
With it being thin, light, and durable, how exactly is the handmade Washi made?
Let's look through the actual making process using paper mulberry as the ingredient.
This time, we will introduce the paper making procedure, along with the works you can actually experience at the "Handmade Washi Experience" workshop held in Ozu Washi.
①Cutting the barks out of the Mulberry tree and steaming it.
Washi making begins by cutting out wood from withered mulberry trees.
The mulberry tree is a plant of the family Moraceae, and it is characterized by its long fibers which is about 5 to 6 millimeters long on average.
To make the bark peeling easier, the cut out woods will be bundled together and steamed.
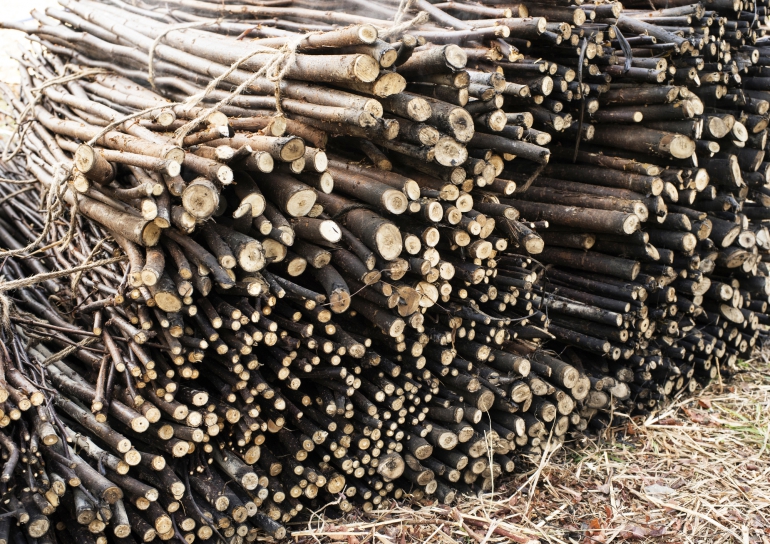
These trees will transform into a Washi
②Peeling the barks, and soaking it.
Once the steaming process is done and the bark becomes soft enough, the peeling procedure begins.
There are 3 layers in a mulberry bark, which are the "Kurokawa", "Amakawa", and "Shirokawa". Out of these, the Amakawa and Shirokawa will be used for Washi making. Also, barks may be dried for preservation purposes.
The mulberry bark after peeling off the epidermis
The barks are not white enough at this point.
In order to make it purely white, it has to be soaked in pure water.
This bleaching procedure is called the "Sarashi", and you can see the barks gradually whiten on its own in the water without any need for adding human touch.
At well-known Washi production regions, the scenery of barks being placed inside the river waters is a traditional and familiar sight seen in winter, but the use of water tanks are replacing the role of the rivers recently.
If it's still not white enough, there are cases when sun drying procedures may be added to further enhance the whiteness from the decolorization effect of the ultraviolet rays.
③The boiling process.
A boiling procedure using soda, lime, and wood ash saps follow next to soften the barks even more.
Once this is done, it will be placed again in running water to skim off the scums to further pursue the whiteness.
④Removing small contaminants.
From here on, barks will be soaked in water to remove small contaminants and black spots, which is all done by hand.
This work requires extreme patience, but is essential to achieve the pure whiteness of Washi.
⑤Loosening the fibers.
After repeating these bleaching, sun-drying, and dust removal procedure, finally the mulberry fiber is whitened enough to meet the high standards of Washi, where it is then beaten with a special stick to loosen up the fibers.
The actual stick and stand used during this process is exhibited in Ozu Washi.
The stick and stand used to loosen the fiber
Try holding it in your hands and you will notice that the wooden stick is quite heavy, to the extent that barely lifting it up using both of your hands is the best you can hope for.
The artisan handles this stick and beats the fibers with only one hand, and you can experience the extreme physical strength required in the making of Washi.
⑥Making paper material.
Finally, we are able to witness the familiar scene seen in the "Handmade Washi Experience" workshop. Here, the loosened fibers, water, and an adhesive called "Neri (mainly Sunset Hibiscus)" is added and mixed inside a tub called Sukibune.
Making the paper material from blending the Neri with the fibers
Though it's called an adhesive, Neri is not used literally as a glue, but it serves the role of helping the fibers to stiffly entangle with each other.
As for this reason, you will see that the Washi is not made from glueing the fibers, but rather formed by the entanglement of the fibers during the mixing process.
⑦Paper making
The paper materials will be scooped up by using a tool called "Suketa".
There are mainly two ways to form a paper, which are the "Nagashi-Suki" and "Tome-Suki".
The method you can experience at the workshop of Ozu Washi is the "Nagashi-suki", which is currently the mainstream way of Japanese paper making.
After scooping the paper raw materials using the Suketa, it will be finely shook back and forth, left and right parallely, to enhance the entanglement of the fibers.
The tip for this is to shake is parallelly
When you actually try this, you'll be surprised by how difficult this process is.
Mr. Takagi, who also serves as the instructor of this workshop told us, "Only a one in a hundred can successfully make a beautiful Washi on their first try."
I have to admit that this must be true, since the second your moving hands are not parallel, wrinkles will start to appear, which then results in the creation of an awkward looking Washi.
Needless to say that concentration is an important factor for this task, you also need a bit of knack since it also requires precise hand movements.
The fibers must be entangled thinly and evenly
⑧Piling the papers on the floor.
A process called "Shito" follows, where the spread Washi is stacked up.
The finished Washi will be quickly peeled off one by one with a steady hand, and piled up on the floor.
Although the Washi is still wet during this procedure, it won't stick to each other upon stacking.
From this, you can understand that each Washi is solidified from the inside, by the tanglement of the fibers.
You can also experience the peeling process of the Washi at the workshop in Ozu Washi
⑨Squeezing and drying
Coming up next is the squeezing process called "Assaku".
At this point, the wetness will be removed for the most part, but it is still not completely dried.
Removing the moisture by using the squeezer
After putting the Washi through the squeezer, the sheets will be peeled off one by one for it to be dried. At the workshop, this will be done on a heated plate, by using a brush to release the air.
There are several other ways to do this, with sun drying also being a typical method.
Drying the Washi on a heated iron plate
We’re finally done when it’s dry
⑩Inspection
Once the Washi is completely dried, the craftsmen carefully checks through each paper.
This inspection procedure is performed at the very end, and if they find any defects, that paper will be sent back to the spreading process for reproduction.
Since Washi is made only from natural raw materials, it can be reproduced as a brand new paper by simply disentangling the fibers.
Although there are other detailed tasks involved in the paper making process, the general flow is as explained above.
Since now you know that the Washi is bleached using plenty of pure water, you can understand that it can only be made in nature-rich regions.
By the way, it is said that only 4 kg of Washi can be made from 100 kg of mulberry barks.
With the yield rate being 4%, which is insignificantly low, its scarcity was definitely a major factor for the Washi to be valued so much.
Various Washi being made all around Japan
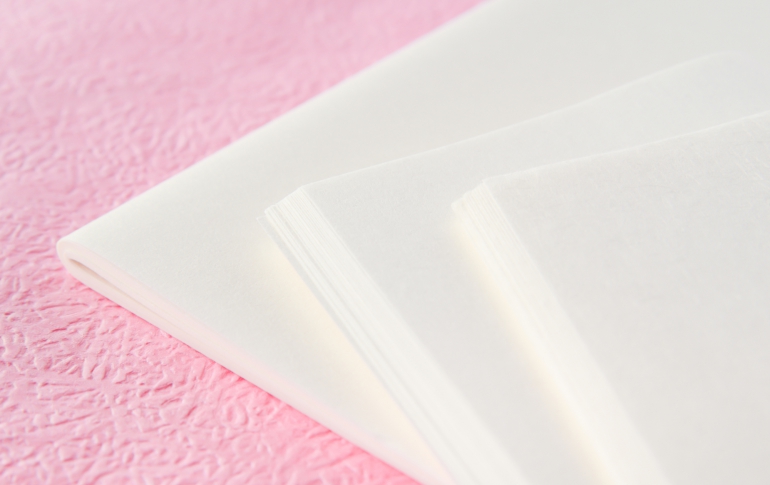
Where is Washi produced?
When speaking of Washi, Mino Washi and Tosa Washi are the most notable ones for the majority of people, but in fact, Washi is made in locations all around Japan from Hokkaido in the north to Okinawa in the south.
This is because raw materials used for Washi making are obtainable nationwide, and highly pure water can be easily accessed in all regions of Japan.
Here, we wish to introduce the Mino Washi, Tosa Washi, and Echizen Washi which are all especially well-known Japanese traditional paper brands.
"Mino Washi", Gifu Prefecture
Mino Washi is designated as a traditional craft product of Mino city in Gifu prefecture.
It is said that Mino Washi was used as a family registration form in A.D.702, which is said to be the oldest paper record existing in Japan and is currently preserved at Shosoin in Nara prefecture.
This means that Mino has a history of actively producing Washi from A.D.702, and valued its beauty and quality since then.
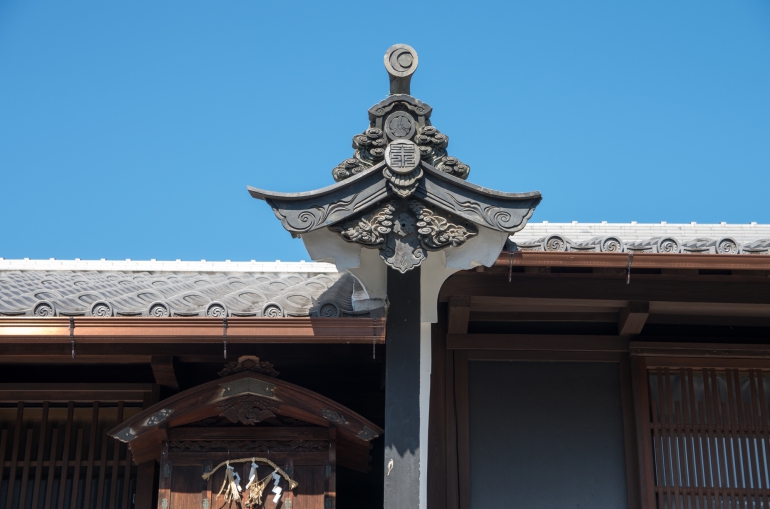
Mino city is known as the “The town where the world rises”
The quality of a Washi is determined not only by its thinness and feeling, but also by the evenness of the patterns of tangled fibers seen when exposed to light.
Mino Washi is known to inherit and pass on the traditional paper making method of Nagashi Suki, in which they implement a technique called “Jyumonji Suki” to create an equal looking fiber entanglement through shaking it vertically and horizontally numerous times..
"Echizen Washi", Fukui Prefecture
Though the Washi made in Echizen is generally called the "Echizen Washi", the spreading technique, materials used, and characteristics are diverse.
Here, we will introduce the most representative Mino Washi known as the "Echizen Art and Craft Paper", which are mainly used as Fusuma paper.
A pattern is created by utilizing water pressure in the “Rakka-shi”
Turning a paper into a work of art is achieved through coloring and drawing patterns, and these processing techniques are the distinctive features of the Echizen Washi.
This can only be accomplished in Echizen, since it has long had an advanced papermaking technology to produce the highest quality Washi in Japan.
Beautiful designs are formed by using various "Suki" spreading techniques, with the "Mizutama-shi", "Rakusui-shi", and "Suiryu-shi" where patterns are drawn using water pressure, and the "Hikkake-shi" in which designs are created on a ground paper using molds.
The art and craft paper implements a two layer structure with the ground paper on the bottom, and the "Uwagake-shi" provided with decoration placed on the top. It has been traditionally used as materials for Fusuma papers and handmade fine arts, and still remains the same today.
"Tosa Washi", Kochi Prefecture
Various kinds of paper are available for Tosa Washi as well, but out of them, the "Tosatengujou-shi" which is often referred to as a "Wing of Mayfly", is well-known as the thinnest Washi in the world. By adding the extreme thinness to the existing features of Washi, it is an optimal choice to use for restorations of artistic works.
Tosa Washi is often referred to as a "Wing of Mayfly" due to its thinness
This super thin paper is created by using a spreading technique not seen in others, where the vertical and horizontal hand movements are more dynamic. With additional force being applied, the paper materials will spread with more energy, allowing it to spread equally. This is how this extra thin paper is made.
Do you want to add an accent to your everyday life? Our recommended Washi goods.
In addition to learning about the history, making, and various kinds of Washi in Japan, Ozu Washi also has a shop which sells numerous products related to Japanese traditional papers.
After deepening your knowledge about the Washi, why not visit the shop and purchase unique Washi goodies to add a traditional Japanese taste to your everyday life?
The line-up has a wide range starting from colorful Yuzen-style "Yuzen-shi" papers, cute looking "Chiyogami" decorative papers, a "Goshuincho Kit" to make your original stamp book, Washi with gradation colors used for making Chigiri-e art, to various other traditional papers such as "Rakka-shi" and Japanese writing papers classified by purpose for Kana writing or Kanji writing, and more. Simply looking at these multicolored diverse collection of Washi will make you excited.
Lastly, allow us to introduce you the especially popular items, best suitable for souvenirs.
Greeting cards made from Washi
<img src="https://s3-ap-northeast-1.amazonaws.com/thegate/2019/11/08/15/46/51/greeting-card.JPG" alt="Greeting Card" /
Why not present someone with a beautiful Mino Washi?
This is a greeting card made from Washi, where the entangled fibers creates a motif.
It is a Mino Washi made 100% from mulberry, and designs of gold fishes and owls are available. When you place it on a glass surface and spray water on it, it will magically stick to the glass, and it surely will be appreciated as a gift for window decoration.
A Fudepen with a gorgeous Yuzen-shi look
The elastic brush tip feature of the Fudepen for a light-hearted Japanese brush writing experience
Ink spreads excellently on Washi, making it well-compatible with Fudepen (Japanese brush pens). With this being said, we strongly recommend you to purchase this pen along with greeting cards and letter paper made from Washi.
The elastic brush tip of a fudepen allows you to enjoy a light writing touch, and you can add colorful Yuzen-shi around the barrel to create a gorgeous Japanese-like brush pen, which will definitely make your mood elevate every time you use it.
Feeling the Japanese culture at your home! The hanging scroll.
To people who wish to implement traditional Japanese culture in their room through interiors, hanging scrolls will be the choice for you.
By choosing a hanging scroll with a simple design, it will surely match any room to create a noble atmosphere. As for this reason, it is a popular gift among foreigners.
With a variety of designs available, enjoy your search for the scroll of your choice
Developed in a way unique to Japan, a summary of the "Washi"
With paper being introduced from the Asian continent to Japan during the Asuka era, "Washi" has evolved technically to fit the lives of Japanese people since its birth. The clean and pure water of Japan allowed this beautiful and limp paper to become a distinctive culture of Japan.
However, traditional items made from this traditional Japanese paper such as Shoji, Fusuma, and books, are not actively produced in Japan these days.
Luckily though, this fact makes us appreciate the value of Washi even more, and everyone is sure to appreciate the excitement of implementing a small bit of Japanese culture in their everyday lives from hiding a Kaishi tissue in a bag, or sending letters in a decorative Pochibukuro envelope made of Washi, and more.
Why not visit Ozu Washi upon your visit to Japan, to discover the attractions of Washi and to meet the Washi goods of your choice.